Cutting Fluids
This article examines the purpose, importance, and types of cutting fluids in CNC machining.
Overview
Cutting fluid is a specially designed substance used in metalworking and machining to act as both a lubricant and coolant. It is typically applied during machining through methods like flooding, fluid jets, or mist spraying.
A good cutting fluid will showcase the following properties:
Thermal Conductivity | This indicates how well it removes heat from both the workpiece and the tool. |
Heat Capacity | A cutting fluid with a higher heat capacity can absorb more heat before it becomes hot or boils. |
Low Viscosity | The low viscosity of a cutting fluid ensures smooth flow and prevents sludge from forming when chips mix with the fluid. |
Non-Corrosive | Your cutting fluid cannot corrode or otherwise damage either your workpiece or cutting tool. |
Corrosion/Oxidation Resistant | A quality cutting fluid should not only avoid being corrosive but also protect parts from corrosion and oxidation. |
Non-Toxic | Given that your cutting fluid will come into contact with humans, choose a cutting fluid or coolant that isn't toxic. |
Chemically Non-Reactive |
Cutting fluids should not react chemically with surfaces they touch, as this can harm the surfaces and degrade the fluid. |
Odorless |
It should be odorless to prevent any lingering smells on the machine or the finished part. |
Transparent/Translucent |
It should be clear enough to allow an unobstructed view of the workpiece. |
Stable | A good cutting fluid should remain stable and not break down quickly during use or storage. |
It’s important to understand what types of cutting fluids are available on the market, the different properties and factors that will impact your machining project, and how to select a cutting fluid that will reduce costs, reduce impact on tools, and best protect your workpiece.
The Purpose of Cutting Fluids
Cutting fluids and coolants are essential for improving the efficiency and quality of machining.
Lubrication
Friction is the main contributor of heat buildup during machining, which can cause surfaces to stick together. Cutting fluids help by forming a thin layer between the chip and the tool, reducing their contact. This lubrication also minimizes tool wear and decreases the energy needed for machining.
Improved Tool Life
Cutting fluids extend tool life by cooling them during machining operations, which minimizes the risk of overheating. By significantly reducing friction, these fluids ensure smoother and more efficient tool performance.
Chip Evacuation
During machining processes like milling and drilling, chips can gather around the cutting area, potentially hindering the operation. Cutting fluids help by removing these chips from the cutting zone.
Cooling
During metal cutting, heat builds up in the workpiece, chips, and cutting tool due to friction and metal deformation. This heat can cause problems like thermal expansion, oxidation, and surface welding. Cutting fluid helps cool the tool and workpiece, preventing these issues.
Corrosion Prevention
Cutting fluids contain rust and corrosion inhibitors that protect machine parts and surfaces from corrosion. Mineral oil-based cutting fluids prevent oxidation by creating a thin protective layer on exposed surfaces.
Improved Surface Finish
Cutting fluids help achieve a smooth surface finish on machined parts by preventing thermal expansion and changes in the workpiece properties.
Types of Cutting Fluids
Cutting fluids are categorized by their phase, composition, source, and application method. They can be generally grouped as follows.
Straight Oils
Straight oils are mineral oils that do not mix with water. Initially, animal and vegetable oils were used as pure lubricants in metal cutting. While they are eco-friendly due to their biodegradability, they are costly and break down quickly. Therefore, they are now primarily used as additives to enhance the lubrication of petroleum and mineral oils.
Mineral oils are made from refining crude oil and are petroleum-based. They often include additives like chlorine, phosphorus, and sulfur to help reduce tool wear.
Soluble Oils
Soluble oils are mixtures made by adding mineral oil to water, typically in a ratio of 1-20% oil to water. These coolants include emulsifiers like sodium sulfate to help oil blend with water, additives to enhance corrosion resistance or act as coupling agents, biocides to stop bacteria growth, and anti-wear additives to improve lubrication.
Soluble oils are the most affordable and widely used cutting fluids in machining. They offer effective cooling and moderate lubrication, making them ideal for light cutting tasks.
Synthetic Fluids
These water-based fluids compete with mineral and petroleum-based oils. They are created by dissolving organic and inorganic chemical compounds in water, along with additives. These additives include lubricants, rust inhibitors, and corrosion inhibitors, which enhance properties like lubrication that might otherwise be reduced by the water content.
Semi-Synthetic Fluids
Semi-synthetic fluids blend synthetic fluids, water-based fluids, and soluble oil emulsions. They consist of 5-50% mineral oil, additives, and chemicals that dissolve in water to create tiny microemulsions. These fluids offer the benefits of both soluble oil and synthetic fluids.
How to Choose the Right Cutting Fluids
Choosing a cutting fluid depends on factors like the type of cutting tool, the material of the workpiece, and the machining operation.
Workpiece Material
Metals are the primary materials that need cutting fluids. Here are some commonly machined metals and their recommended cutting fluids.
- Steel – straight oils with added lubricants
- Alloy steels – mineral oils
- Aluminum – soluble oils or mineral oils without active sulfur (active sulfur stains aluminum)
- Copper – soluble oils
- Stainless steels – straight oils containing excellent extreme-pressure additives
- Cast iron – None
Cutting Tool Type
Carbide tools can become extremely hot, making them prone to thermal shock, where parts of the tool expand unevenly. For these tools, use a synthetic cutting fluid with excellent cooling properties.
High-speed steels heat up, but not as much as carbide tools. Soluble oils and semi-synthetic fluids work well for them.
Machining Operation
Machining operations like turning, milling, forming, and drilling occur at high speeds, requiring significant cooling. These processes need only moderate lubrication and pressure resistance, making synthetic fluids the best choice. Soluble oils can also be used.
For challenging machining tasks like broaching and thread cutting, effective lubrication is essential. These processes occur at low speeds and high pressures, so cutting fluids with superior lubrication and extreme pressure capabilities are necessary. Mineral oils with extreme pressure additives are the ideal choice.
Goal
In addition to these other factors, you'll also want to consider your goal and end-use. Use the table below to identify what the most appropriate metal cutting fluid will be based on the project's priority.
Priority | Recommended Cutting Fluid |
Precision machining | Water-soluble fluids |
Heavy-duty machining (steel, titanium) | Straight oils or emulsions |
High-speed machining | Synthetic or semi-synthetic fluids |
Maintenance and Disposal
Proper cutting fluid maintenance extends tool life, prevents contamination, and cuts costs by ensuring top performance. Equally important is responsible disposal for environmental compliance, making it crucial to follow best practices in fluid management and waste reduction.
Maintenance
Essential steps for maintaining cutting fluid include:
- Accurately monitor concentration levels (typically done with refractometers or chemical titration)
- Keep the pH level between 8.5 and 9.5 to stop bacteria from growing and to keep the fluid stable
- Regularly remove tramp oil to maintain fluid efficiency and lower disposal expenses
- Install filtration systems to remove metal particles and contaminants, which extends the fluid's lifespan
- Provide thorough training so operators can recognize fluid degradation and carry out routine maintenance efficiently
Disposal
To reduce environmental impact and avoid legal issues, follow these practices to comply with environmental regulations:
- Implement recycling programs that prolongs fluid life by filtering and reprocessing coolants, which reduces both waste and costs
- Test coolants for harmful chemicals before disposal (done according to hazardous waste guidelines)
- Invest in coolant management systems that keep fluids in good condition and reduce waste
- Use biodegradable cutting fluids to reduce environmental impact
Frequently Asked Questions
What are cutting fluids in CNC machining?
Cutting fluids, used in CNC machining, are liquids or gases that cool and lubricate the cutting tool and workpiece. They reduce heat, decrease tool wear, and enhance the surface finish of the machined part.
Why are cutting fluids important in CNC machining?
Cutting fluids are essential because they cool down the heat from machining, reduce friction between the tool and the workpiece, and protect the tool from wear. They also help remove chips and enhance the quality of the finished part.
What are the different types of cutting fluids?
Cutting fluids come in four main types: water-based, oil-based, synthetic, and semi-synthetic. Each type has unique properties and uses.
How do water-based coolants work?
Water-based coolants are mainly used for their ability to cool. They include additives that improve lubrication and stop corrosion. They are ideal for machining tasks that produce a lot of heat.
What are the advantages of oil-based coolants?
Oil-based coolants offer superior lubrication and effectively minimize friction between the cutting tool and workpiece. They are ideal for machining tasks that need high lubrication but minimal cooling.
What are synthetic coolants?
Synthetic coolants are specially formulated fluids that provide both cooling and lubrication. They are crafted to deliver top performance in various machining tasks and are frequently used in high-precision settings.
What are semi-synthetic coolants?
Semi-synthetic coolants combine water-based and oil-based elements, providing effective cooling and lubrication. This makes them ideal for various machining tasks.
How do cutting fluids improve tool life?
Cutting fluids extend tool life by reducing heat and friction during machining. This minimizes wear and damage, keeping the tool sharp and effective for longer.
What factors should be considered when selecting a cutting fluid?
When choosing a cutting fluid, consider the material you're machining, the type of operation, the desired surface finish, and the application's specific needs. Ensure it is compatible with your machine and environmentally friendly.
How are cutting fluids maintained and disposed of?
To keep cutting fluids effective, regular maintenance is necessary. This involves checking concentration levels, removing contaminants, and replacing fluids when needed. Proper disposal is crucial to avoid environmental harm and meet regulatory standards.
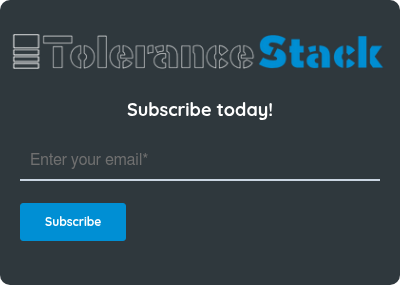
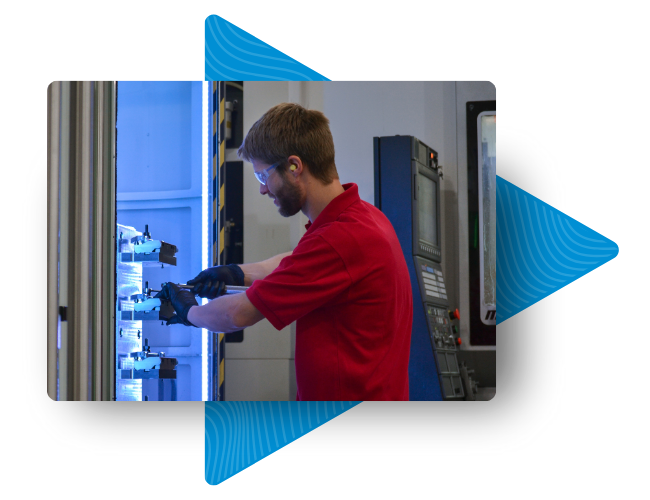
Let's connect
Want to learn more about our CNC machining services? Schedule a time to speak with our team.