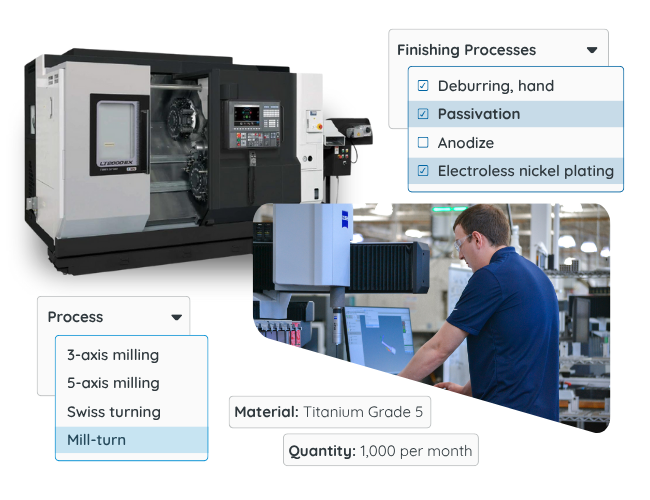
CNC Machining for High Volume Production
When your team is ready to ramp up production from the 100s to the 1000s, we're ready with advanced machining operations that are equipped with automation and lights-out capabilities to leverage cost savings and deliver consistent quality.
High Volume CNC Machining
When you’re ready to grow, you need full-scale, automated production. We tackle high-volume production with advanced CNC machines, machining automation, and lights-out equipment for 24-7 production.
When your production is ready to ramp up from the hundreds to the thousands, our systems, processes, and team of experts are in place to ensure that every component produced maintains the highest standards of precision and reliability.
Flexible Manufacturing Solutions
Our multi-machine flexible manufacturing solutions enable high-mix machining for high-volume production.
Spread across two Fastems systems, seven 5-axis mills, and over 100 pallets, we can support orders in the 100s and 1000s, as well as develop processes that reduce setups, decrease cycle times, improve quality, and cut down on costs.
- High repeatability
- Automated, lights-out production
- Eliminated setup
- Scalable solutions
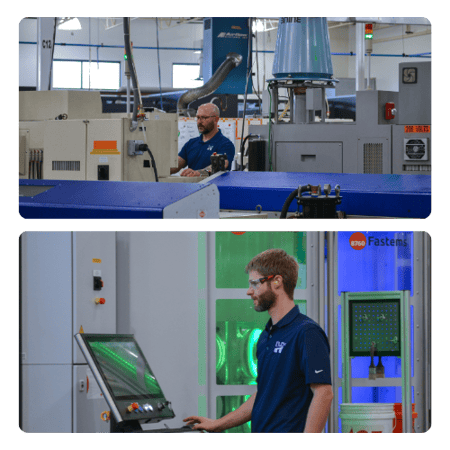
CNC Machining available for High Volume Production
We offer a full suite of CNC capabilities -- including 3, 4, and 5-axis milling, Swiss-style turning, conventional turning, and mill-turn machining -- to support high volume production.
Our team specializes in parts with complex geometries, tight tolerances, and rapid iteration cycles.
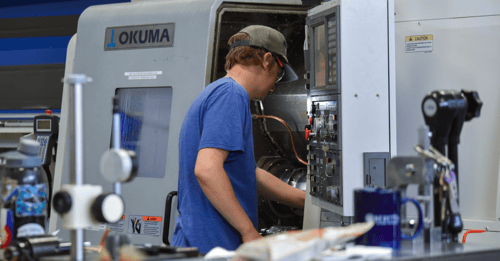
CNC Machining for Low Volume Production
Release your design into production with the support of a committed partner, a tailored production process, and a streamlined manufacturing experience.
Additional Capabilities
Design for Manufacturability
Our feedback process increases product quality, shortens lead times, and keeps customer costs low by optimizing your product and automating the production process whenever possible.
When you partner with our team, you get more than a machined part. You're collaborating with us to create a unique manufacturing solution that's optimized for your needs.
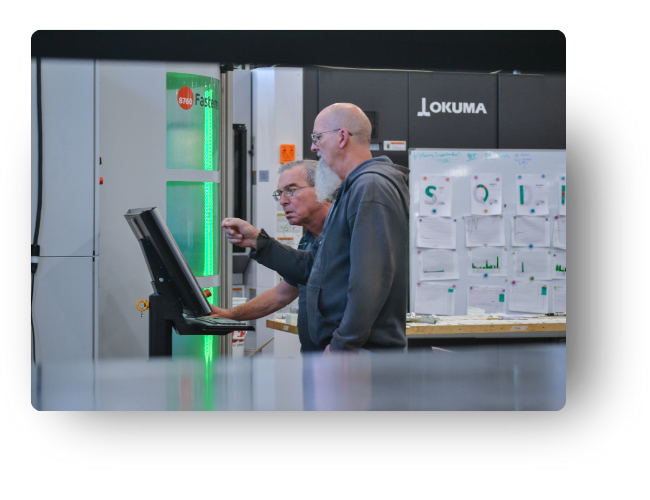
Quality Control
We deliver industry-leading levels of quality by using best-in-class inspection technology, continuously improving our QMS, and aligning our practices with international quality standards.
Our compliance, systems, and processes allow us to carefully and responsibly meet our customers' needs with industry-leading levels of excellence.
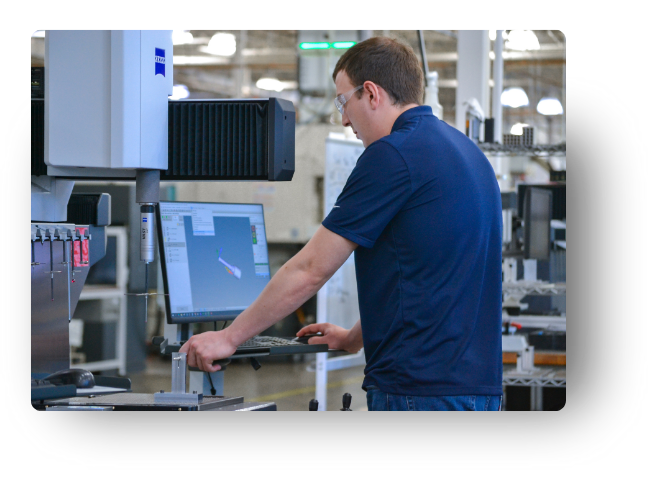
Surface Finishing
A machined component's surface finish is crucial when it interacts with other components.
We offer a variety of surface finishing methods, both in-house and through our supplier network, to improve your part's durability, surface finish, and aesthetic appearance.
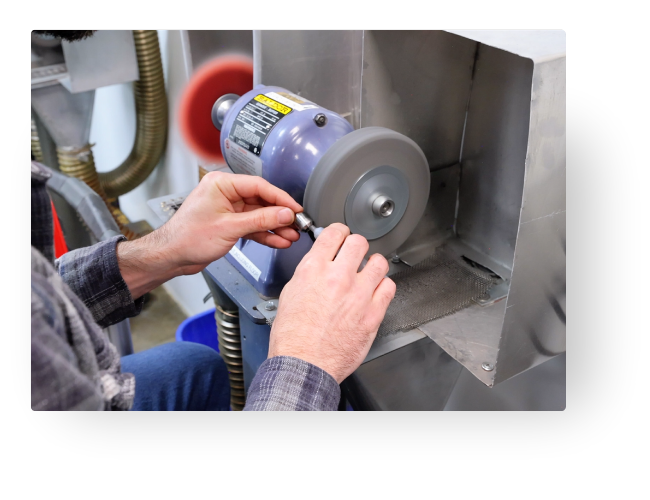
Complex Assembly
With our ISO 13485:2016 and AS9100 certified facilities, we supply complete finished device assembly for the medical device, aerospace, and industrial sectors.
Our mechanical and electro-mechanical assembly services free up our customers' time, personnel, and resources so they can focus on what matters most.
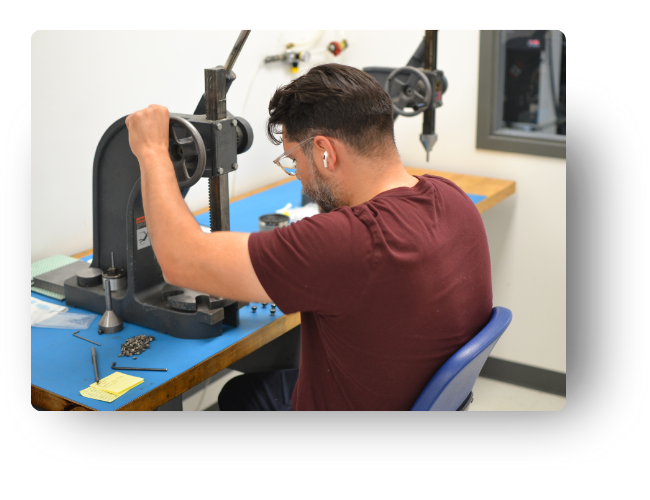
Inventory Monitoring
We combine our ERP, a seamless quoting system, and our proprietary manufacturing software to supply proactive inventory monitoring and management.
Our inventory management solutions are an efficient, cost-effective way to ensure you never go without parts, avoid lead times, and help you deliver your product or service with the shortest turnaround time possible.
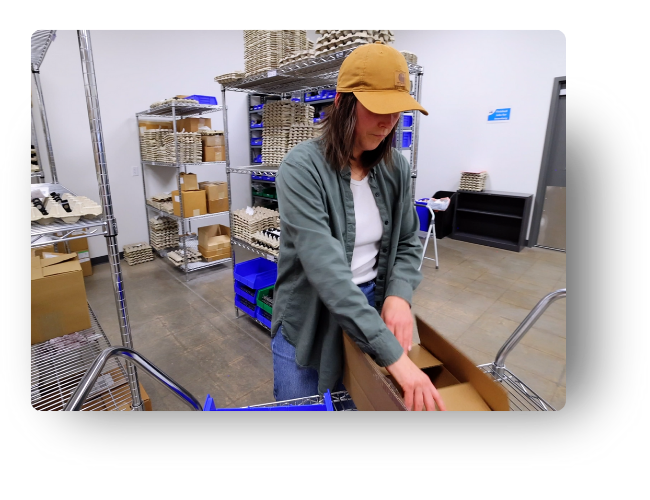
CNC Machining Materials
CNC Machining FAQs
What industries do you support?
Hirsh has a long history of supporting the industrial, automotive, aerospace, medical device, biotechnology, and scientific instrument sectors.
What tolerances can you hold?
General tolerances on metals can be held to +/- 0.005" (+/- 0.127 mm) in accordance with ISO 2768 unless otherwise specified. Plastics and composites can be +/- 0.010”.
Hirsh can also machine and inspect to tight tolerances, including sub +/- 0.001" tolerances, per your drawing specifications and GD&T callouts.
Can you assist with design optimization for machining complex parts?
Yes, in fact, it’s our team’s preference that we support your part’s production with DFM before moving into production.
Our DFM is most effective when it’s requested before a design is finalized. We can still provide design optimization feedback even after a design has been finalized, though. Contact our team as early in the manufacturing process as possible to achieve the biggest time and cost savings.
How can I request a quote from Hirsh?
Easy! Just submit an RFQ through our website.
What file formats do you accept for part uploads?
We accept STEP, STP, SLDPRT, IGS, X_T, PDF, JPG, and PNG file formats.
For the fastest turnaround time on quotes, please include both a CAD model and a detailed, reviewed technical drawing for each part that you want quoted. This enables our team to build a comprehensive quote and move into production as quickly as possible.
What machining capabilities do you have?
Milling: 3-, 4- and 5-axis CNC milling options for your most complex and intricate components
Turning: Swiss and multi-turret turning centers with live tooling and barfeeders to support lights-out production.
Flexible Manufacturing Solutions: two Fastems systems, seven 5-axis mills and over 100 pallets to support production in the 100s and 1000s; reduced setups and shorter cycle times improve quality and cut down on costs.
Here is a comprehensive list of our CNC machines.
What types of materials do you machine?
We work with a wide variety of metal and plastic materials, including medical-grade plastics.
Explore the Material Index to learn more about the types of metals and plastics we machine.
What finishing options are available for machined components?
Hirsh offers a range of surface finishing methods, both in-house and through our supplier network. These finishing options are designed to improve your part’s durability, finish, and aesthetic appearance.
Here is a full list of our surface finishing options for CNC machined parts.
Can you assemble parts at your facility?
Yes, we offer both mechanical and electro-mechanical assembly services.
What certifications or industry standards do you adhere to?
Hirsh Precision is ISO 13485 and AS9100 certified, and our QMS is compliant with ITAR, EU REACH, EU RoHS, and EU CMRT.
Our approved manufacturing partners also adhere to a variety of industry standards, including: ISO 9001, ISO 13485, ISO 14001, AS9100, IATF 16949, and NADCAP.
Learn more about Hirsh’s approach to quality.
What inspection options do you offer?
We offer several different inspection options, including a standard FAIR, a certified inspection report (CIR), AS9102C FAIR, APQP, PPAP, and SPC.
You can read more on our Quality page.
What metrology equipment do you have?
Hirsh maintains a wide range of inspection technology and equipment, including many CMMs, multiple styles of visual inspection systems, in-house calibration for hand tools and gages, and “Z” class gage pins at every machining center.
Machining and Inspection Capabilities
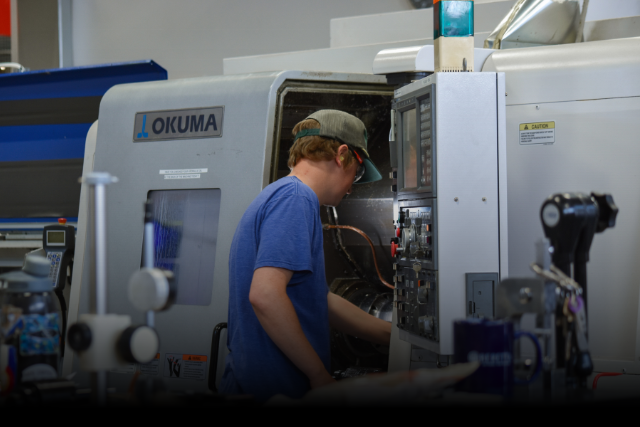
CNC Turning and 5-Axis Milling
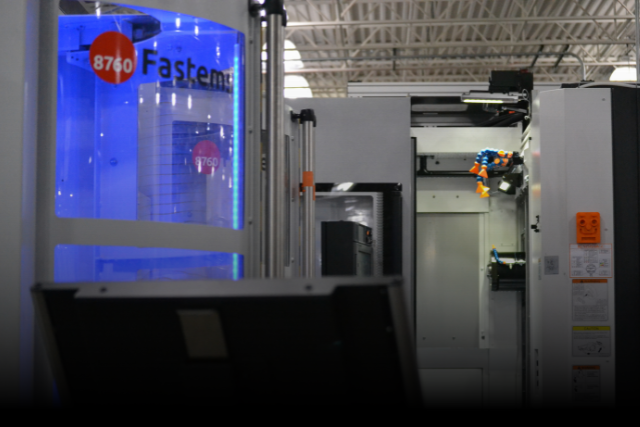
Flexible Manufacturing
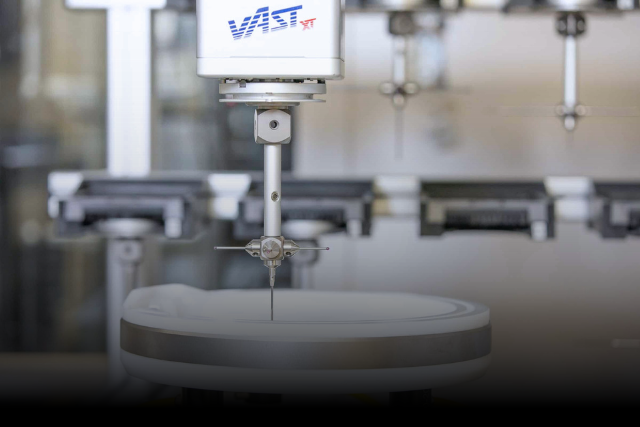
Quality Control
.png?width=612&height=406&name=%232%20-%20Material%20Sourcing%20Services%20(1).png)
OEM Collaborates with Hirsh to Automate & Scale Production
Challenge: our customer couldn't scale production to meet increased demand due to a manual process that bottlenecked their operations
Solution: we relieved the customer of their in-house process and developed both a new machine and an automated process to increase throughput, process consistency, and part quality
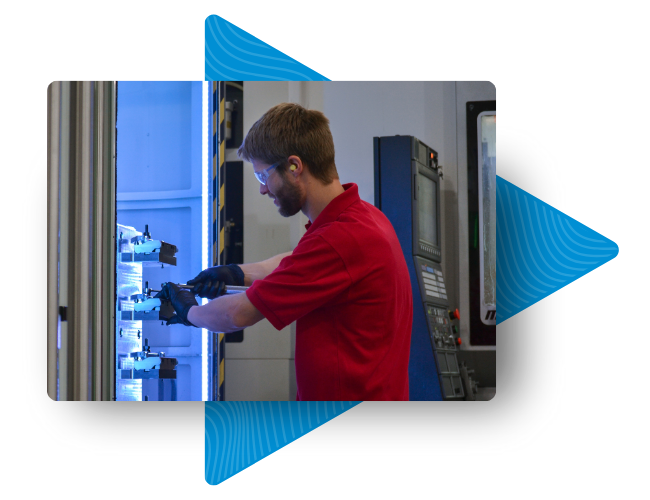
Let's connect
Want to learn more about our CNC machining services? Schedule a time to speak with our team.