Machining Tolerances
This article covers CNC machining tolerances, types, and sources of variation to ensure precise, high-quality parts that fit and function correctly in your projects.
Table of Contents
Overview
Tolerances refer to the total allowable deviation from a dimension's basic value, and ensure a part fits and functions correctly (ASME).
Tolerances are checked during the quality inspection after CNC machining. They guide the choice of manufacturing methods needed for a part. Tighter tolerances might need advanced equipment or extra processing to meet the required dimensions.
For CNC machined parts, various types of tolerances can be defined and used.
Types of CNC Machining Tolerances
In CNC machining, "tolerance" refers to how precisely a machine can shape a part. CNC machines are incredibly precise, with some achieving an accuracy of ± 0.0025mm, about a quarter of a human hair's width. However, tolerances differ among machines and are typically set by the manufacturer, with 0.02mm being a common standard. CNC service providers also inform customers about their machines' tolerances.
In design and manufacturing, tolerance refers to the allowable range of size variations for a part that still ensures it works properly. Designers set these tolerances based on the part's function, fit, and form. Tolerances are vital for parts that connect or interact with others. For instance, parts of an electric engine require tighter tolerances than a door handle because they have more features that need to fit together precisely. Tolerances are indicated by a number next to the relevant dimension.
Standard Tolerances
Standard tolerances are widely used to define how much a CNC machined part's dimensions can vary. These tolerances might represent what a machine shop can produce without extra cost or serve as a general variation applied to an entire drawing, as noted in a title block or note, unless specified otherwise in the drawing or on certain features.
Limit Tolerances
A limit tolerance is the specified minimum and maximum dimension allowed on a drawing. Also known as limits of size, these provide the upper and lower size limits for a feature. This makes it easy to quickly check if a measured dimension falls within the tolerance zone, without needing to calculate boundary dimensions from tolerance values.
Unilateral Tolerances
Unilateral refers to something related to one side. In terms of tolerances, it means the tolerance is applied in only one direction, either plus or minus. In GD&T, this is called an unequally disposed tolerance and is marked with a U symbol. Typically, unilateral tolerances are used at maximum material condition (MMC).
Bilateral Tolerances
Bilateral refers to something involving two sides. In terms of tolerances, it means that both the positive and negative limits are considered for a specific measurement. This provides the smallest and largest acceptable sizes for that measurement. The tolerance can be equal on both sides or vary between them.
Sources of Variation in Machined Components
CNC-machined parts are not flawless. Variations among these parts are expected and result from several factors.
Types of Raw Material
Harder materials allow for tighter tolerances because they maintain their shape and resist deflection during machining. They offer greater dimensional stability compared to softer materials. Additionally, materials with a lower coefficient of thermal expansion (CTE) are less affected by temperature changes, enabling even tighter tolerances.
Condition of the Workpiece
Using uniform and precise stock materials significantly minimizes variations. The quality of your raw materials directly affects the quality of your final product.
CNC Machine Used
While more expensive machinery doesn't always guarantee higher quality parts, it often does. Machines that maintain tighter tolerances are typically built with superior raw materials and advanced programming, ensuring precise tooling alignment during milling.
Tooling
Without precise and accurate tooling, achieving tight tolerances is impossible, regardless of how well you prepare your material.
What are machining tolerance?
Machining tolerances define the acceptable range of size and shape variations in a machined part. They ensure that even with slight differences, the part remains within acceptable limits.
Why are machining tolerances important?
Machining tolerances are crucial for ensuring parts fit and work properly in their applications. They guarantee consistency, quality, and the ability to interchange parts.
What are the different types of machining tolerances?
Machining tolerances include dimensional (linear and angular), geometric (like flatness, straightness, and roundness), and surface finish tolerances.
How are machining tolerances specified?
Engineering drawings use symbols and numbers to define machining tolerances, showing the acceptable range for dimensions and shapes.
What factors influence machining tolerances?
Machining tolerances are affected by the material, the machining process, the CNC machine's precision, and the tools used.
What is the difference between tight and loose tolerances?
Tight tolerances mean parts are made with high precision and accuracy due to less variation. Loose tolerances allow more variation, which can save costs but may lead to less precise parts.
How do machining tolerances affect manufacturing costs?
Tighter tolerances increase manufacturing costs because they require more precise machining, better tooling, and extra quality checks. On the other hand, looser tolerances can lower costs but might affect part quality.
What is the role of GD&T in machining tolerances?
Geometric Dimensioning and Tolerancing (GD&T) is a system that defines and communicates machining tolerances. It uses symbols to indicate the acceptable variations in part shapes, ensuring precision and uniformity.
How are machining tolerances measured and inspected?
We use tools like calipers, micrometers, CMMs, and optical comparators to measure and inspect machining tolerances, ensuring parts meet the required standards.
What are common challenges in achieving tight machining tolerances?
Achieving precise machining tolerances can be difficult due to tool wear, thermal expansion, machine vibrations, and material properties. To address these issues, ensure regular machine maintenance, plan carefully, and use high-quality tools.
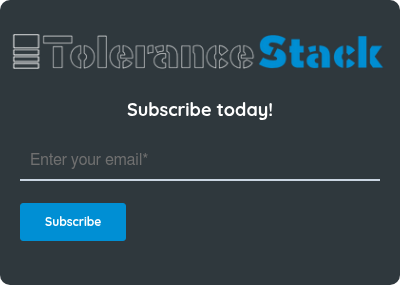
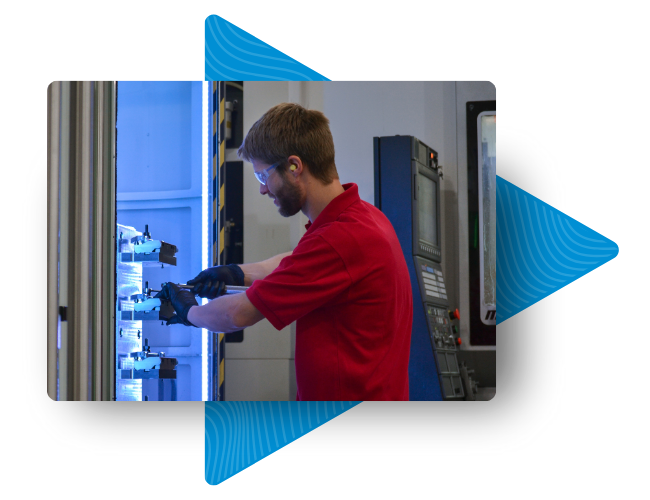
Let's connect
Want to learn more about our CNC machining services? Schedule a time to speak with our team.