Post-Processing
This article provides an overview of post-processing options for metal components and guides you in choosing the right operations for your machining project.
Table of Contents
Overview
Post-processing operations enhance material strength, add anti-corrosive properties, and improve surface smoothness. The most common post-machining processes are heat treatments and surface treatments.
Using the right heat treatment methods and surface finishes enhances the smoothness, appearance, and functionality of CNC machined parts.
Heat Treatment Methods
Heat treatment is a crucial step in CNC machining metal parts. It involves carefully heating and cooling the material to achieve specific properties. This process changes four key properties of metal parts: hardness, strength, toughness, and ductility.
Not all heat treatments are the same. The right method depends on the material's composition, the part's size, and the desired final properties.
Heat treatment aims to create a specific microstructure that imparts desired material properties to your parts, and can be applied to metal alloys at different stages of the CNC machining process, either before or after machining your parts.
- Annealing
- Tempering
- Stress Relieving
- Quenching
- Case Hardening
- Through Hardening
-
Annealing
Annealing involves heating metal to a high temperature and then cooling it slowly to achieve the desired structure. This process is typically used on all metal alloys after they are formed and before any further processing to make them softer and easier to machine. Unless specified otherwise, most CNC machined parts will have the properties of annealed material.
Purpose: to improve the machinability of the metal alloy
Compatible Materials: steel, stainless steel, cast iron
-
Tempering
Tempering involves heating the part at a lower temperature than annealing, typically after quenching mild steels (1045 and A36) and alloy steels (4140 and 4240). This process reduces brittleness and enhances mechanical performance.
Purpose: to release residual stress from mechanical deformation or temperature increase during processing
Compatible Materials: steel, stainless steel, cast iron
-
Stress Relieving
Stress relieving heats the part to a high temperature, lower than annealing, and is typically done after CNC machining to remove residual stresses from manufacturing. This process ensures parts have more consistent mechanical properties.
Purpose: to reduce brittleness after quenching
Compatible Materials: mild steels, alloy steels, tool steels
-
Quenching
Quenching involves heating metal to a high temperature and then quickly cooling it, usually by immersing it in oil or water, or by using cool air. This rapid cooling solidifies the changes in the metal's structure, making it extremely hard.
Purpose: to increase the hardness of the metal alloy
Compatible Materials: mild steels, alloy steels, tool steels
-
Case Hardening
Case-hardening, also known as carburizing, is a heat treatment that strengthens the metal's surface while keeping the inner metal soft. This process involves adding carbon or nitrogen to low-carbon alloys at high temperatures to enhance their hardenability. The surface finish can be applied either before or after the CNC machining process.
Purpose: to improve surface toughness and increase corrosion resistance
Compatible Materials: steel alloys, copper, aluminum, brass
-
Through Hardening
Through hardening is different from case hardening because it strengthens the entire alloy, not just the surface. This is done by adding carbon to the alloy and cooling it quickly in brine, water, or oil.
Purpose: to enhance the wear resistance and fatigue strength
Compatible Materials: alloy steels, tool steels, stainless steels
Surface Finishing Methods
Surface finishing methods protect and enhance the look of a machined component's surfaces. These methods may add or remove material, or use heat, electricity, or chemicals to alter a part's surface finish.
CNC surface finish and finishing methods are crucial when your part interacts with other components. For instance, ball bearings are designed to minimize rotational friction and support loads. As the races rotate, the balls also turn due to their contact. If the surfaces of the balls or races are not finished correctly, friction increases, leading to more wear and a shorter lifespan, even if the components meet geometric tolerances.
Media Blasting
Media blasting uses compressed air or water to shoot abrasive materials, known as "media," at high speeds onto a surface. This process cleans and prepares the surface for further treatment or finishing.
The type of abrasive material chosen for media blasting varies based on the task and the results you want to achieve.
Purpose: to achieve a smoother surface
Compatible Materials: most metals and plastics
Black Oxide
Black oxide is a coating applied by dipping a part into a sodium hydroxide and potassium nitrate solution. This process creates a black, smooth finish that enhances corrosion and wear resistance.
Purpose: to improve corrosion and wear resistance
Compatible Materials: mild steels, carbon steels, stainless steel, copper
Powder Coating
Powder coating involves using powdered plastic mixed with chemical agents like pigments and additives to create a strong finish on metal parts.
The powder is sprayed onto a part and sticks due to an electrostatic charge. The coating tool charges the powder particles while the part is grounded, drawing the particles to it. The part is then baked, turning the powder into a solid, durable, and corrosion-resistant coating. This process allows for various pigments and finishes. Sometimes, parts are preheated before spraying.
Purpose: to increase strength and provide a good base for dyeing
Compatible Materials: aluminum, stainless steel, steels, copper, brass, zinc
Electroless Nickel Plating
Electroless nickel plating is a technique that adds a nickel layer to a part's surface. This enhances the part's corrosion and wear resistance, as well as increases its hardness.
Purpose: a cost-effective way to improve surface finish
Compatible Materials: aluminum, stainless steel, mild steels, copper, brass, titanium
Eletropolishing
Electropolishing is a process used to improve the surface finish of metal parts. It involves the removal of a thin layer of material from the surface of a metal object using an electrochemical process.
Purpose: to achieve an even, shiny surface that’s corrosion resistance and highly weldable
Compatible Materials: stainless steel, aluminum, copper, brass, nickel alloys
Passivation
Passivation treats metal surfaces with an acid solution to remove free iron and contaminants, restoring a thin, protective oxide layer. This layer shields the metal from environmental reactions, reducing corrosion risk. It is often used on stainless steel and other metals to enhance resistance to rust, stains, and deterioration.
Purpose: to improve corrosion resistance
Compatible Materials: stainless steel, aluminum, titanium
Anodizing
Anodizing creates a thin layer on metal surfaces, offering protection against corrosion and wear. It only works with aluminum and titanium.
In Type II and Type III anodizing, the part is placed in a diluted sulfuric acid solution, and an electric voltage is applied. This causes a reaction that turns the surface into hard aluminum or titanium oxide. Masks can be used on areas that need to stay conductive or have precise dimensions, like threaded holes, to prevent anodizing. The anodized parts can also be dyed in various colors before sealing.
Type II anodizing, also known as "standard" or "decorative" anodizing, creates coatings up to 25 μm thick. The thickness varies by color: 8-12 μm for black-dyed parts and 4-8 μm for clear parts. This process is ideal for achieving a smoother surface, offering good corrosion resistance and some wear resistance.
Type III anodizing, known as "hardcoat" anodizing, creates coatings up to 125 μm thick, with a standard thickness of 50 μm. This process forms dense layers that offer superior corrosion and wear resistance, ideal for functional uses. It requires more precise control than Type II anodizing, involving higher current density and maintaining the solution temperature near 0 degrees Celsius, which increases the cost.
Adjusting the electric current, anodizing time, solution consistency, and temperature allows you to create coatings with varying thicknesses and densities.
Purpose: to impart a shiny, aesthetic finish that improves corrosion resistance
Compatible Materials: aluminum, titanium
Galvanizing
Galvanizing involves dipping steel into molten zinc. This process coats the steel with layers of zinc-iron alloy and zinc metal. The zinc reacts with the steel's iron content, forming a uniform, thick protective layer.
Purpose: to improve the part’s corrosion resistance
Compatible Materials: mild steels, carbon steels, iron
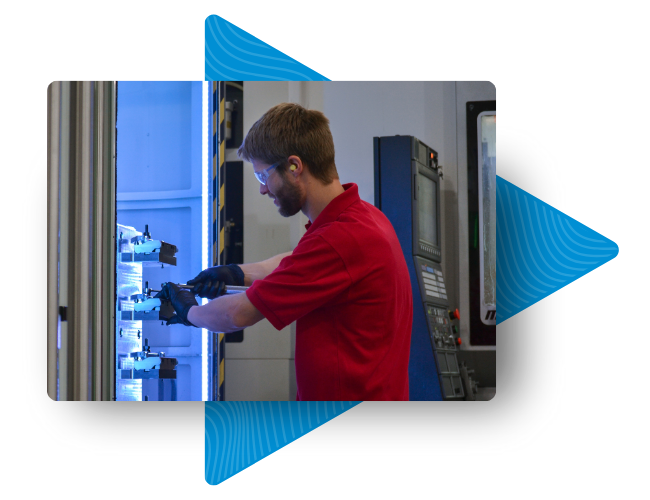
Let's connect
Want to learn more about our CNC machining services? Schedule a time to speak with our team.