Material Selection
This article outlines the key considerations for choosing the right material for a CNC machining project, including the part's application and the material's essential properties.
Table of Contents
Overview
Broadly speaking, the material selection process for your CNC machining project should follow these steps:
Step 1: Determine material requirements
Evaluate the material's functionality, electrical properties, strength, and hardness to ensure it fits your project needs. Additionally, consider the environment where the part will be used and the conditions it will face.
Step 2: Create a list of material options
Organize all the materials that meet your requirements, including your design specifications.
Step 3: Choose the most appropriate material
Select the material that meets most of your needs. Sometimes, you may need to prioritize a material with better machinability over a cheaper option to maintain part quality.
Design and regulatory requirements are the basis of your material selection process, but they can leave you with several material options to choose from. To make the best choice, consider the material's properties, machining needs, finishing requirements, and procurement factors.
By thoroughly evaluating these factors, you can identify the most cost-effective material that guarantees high-quality machining and reduces unnecessary delays in your operations.
Project Requirements
As it relates to your project, here are the key factors you need to consider when selecting the appropriate material.
Part Application
Choosing the right material for CNC machining
is crucial, and different applications require different materials.
The material's physical properties, like tensile strength, strength-to-weight ratio, crack resistance, rigidity, or flexibility, depend on its application. Heavier materials can handle more stress, but for weight-sensitive uses, choose lighter materials with a strong strength-to-weight ratio.
For example, aerospace parts must be lightweight, unlike parts for structural support. Aluminum 3.3211 is often used in aerospace because it has a strong strength-to-weight ratio.
Machining Conditions
The final application of your part will guide many of your material choices, but first, the raw material must undergo the machining process.
Machining rates, also known as speeds and feeds, determine how fast material is removed. Each material has specific machinability traits, like hardness and melting point, that affect how quickly it can be processed, how heat is handled, and how chips are cleared.
The material you choose impacts how quickly your cutting tools wear out. Some materials, like high-temperature alloys, can cause more wear, requiring special tools and increasing costs.
Finishing Requirements
Don't be fooled by the word "finishing;" you need to carefully consider your parts' finish early in the design process, not as an afterthought. This helps avoid compatibility issues between your chosen material and the necessary surface process.
If your project requires a specific surface finish, choose a material that can be easily machined to meet those needs. Materials like aluminum and plastics can achieve a smooth finish effortlessly, while others, like cast iron, may require additional steps to reach the desired quality.
Check if the plating type matches the base material. For example, if nickel plating is needed, aluminum might not be the best choice. Instead, use stainless steel, which works well with nickel plating, ensuring you select the right material.
Material Attributes
Your part will have specific applications and environmental conditions that need to be taken into account when selecting a material.
For instance, parts for electrical use should conduct electricity well, like copper or silver. If used in aeronautics or aerospace, the material should maintain its shape under stress.
Mechanical Attribute
Strength
Strength reflects a material’s capacity to resist forces that attempt to deform or fracture it and is typically measured in terms of stress, which is force per unit area. Stress is typically represented in megapascals (MPa) or pounds per square inch (psi).
Mechanical Attribute
Hardness
A material's resistance to deformation, scratching, or indentation. Harder materials are more wear-resistant but may be more challenging to machine.
Mechanical Attribute
Ductility
A material’s ability to deform under tensile stress, often characterized by its ability to be stretched into a wire. Ductile materials are less likely to fracture under stress.
Mechanical Attribute
Impact Resistance
A material’s ability to withstand sudden and forceful impacts without breaking or shattering.
Thermal Attribute
Thermal Conductivity
A material’s ability to conduct heat. Materials with high thermal conductivity are essential for applications where heat dissipation is crucial.
Thermal Attribute
Thermal Expansion
The degree to which a material expands when heated. Materials with low thermal expansion are preferred for applications requiring high dimensional stability across temperature changes.
Thermal Attribute
Heat Resistance
A material’s ability to maintain its properties at elevated temperatures. Materials with high heat resistance are necessary for high-temperature applications.
Electrical Attribute
Electrical Conductivity
A material’s ability to conduct electricity. Materials with high electrical conductivity are used in applications requiring efficient electrical transmission.
Electrical Attribute
Dielectric Strength
The maximum electric field a material can withstand without breaking down. Materials with high dielectric strength are essential for insulating applications.
Electrical Attribute
Electrical Resistivity
The measure of how strongly a material opposes the flow of electric current. Materials with high resistivity are used in applications requiring electrical insulation.
While design and industry regulations are crucial, consider these procurement factors when selecting a material for your machined component, which can help reduce unnecessary costs and affect your lead times.
Raw Material Cost
The cost of materials is a key factor in procurement. High-end aerospace alloys can be expensive, but more affordable options like plastics are available.
Machining Cost
The machining expenses for each material should be taken into account as well. Certain materials may demand additional time and labor to machine effectively, thus affecting the overall cost of machining.
Availability
When selecting materials, consider their availability. Some materials might be hard to find or take longer to get, which could delay your project. Make sure the material you choose is available within your required timeframe.
Lead Time
Consider the project's timeline as well, as the lead time for certain materials can significantly affect your material selection process. Some materials may have longer lead times than others, potentially causing delays in your overall project schedule.
Choosing a material with more advanced properties than needed for your application can unnecessarily raise the cost of your CNC machined parts.
To minimize cost, select the material with the lowest cost that has properties that fulfill your design requirements.
Here is a table that summarizes how the cost of a part varies based on some of the most common materials.
Cost | Metals | Cost | Plastics |
$ | Aluminum 6061 | $ | POM (Delrin) |
$$ | Alloy steel 4140 | $$$ | ABS |
$$ | Aluminum 7075 | $$$ | Nylon |
$$$ | Brass C360 | $$$ | Polycarbonate |
$$$$ | Stainless Steel 304 | $$$$ | PEEK |
What factors should be considered when selecting a workpiece material for CNC machining?
When choosing a workpiece material, think about its strength, hardness, and toughness. Also, consider how easy it is to machine, its cost, availability, and any specific needs like corrosion resistance or thermal stability.
What are the most common materials used in CNC machining?
CNC machining commonly uses materials like metals (aluminum, steel, stainless steel, brass, titanium), plastics (ABS, polycarbonate, nylon), and composites.
How does the material's machinability affect the CNC machining process?
Machinability is the ease with which a material can be cut, shaped, and finished. Materials with high machinability need less cutting force, offer better surface finishes, and extend tool life. Conversely, low machinability can cause more tool wear, longer machining times, and increased costs.
What is the importance of material hardness in CNC machining?
The hardness of a material impacts tool wear and precision. Harder materials are tougher to machine and may need special tools and methods. Softer materials are easier to machine but might lack the strength and durability needed for some uses.
How do thermal properties of materials impact CNC machining?
Thermal properties, like conductivity and expansion, affect machining. High thermal conductivity helps materials release heat efficiently, minimizing the risk of damage. High thermal expansion may need adjustments for size changes during machining.
What role does material cost play in selecting a workpiece material?
Choosing the right material for a workpiece involves considering cost. High-performance materials can offer better qualities but often come at a higher price. It's crucial to balance cost with performance needs to ensure efficient manufacturing.
How does corrosion resistance influence material selection for CNC machining?
Corrosion resistance is essential for parts in tough environments or exposed to chemicals. Stainless steel, titanium, and some plastics provide excellent protection, making them ideal for use in marine, chemical, and medical fields.
What are the challenges of machining composite materials?
Composite materials like carbon fiber-reinforced polymers are strong yet lightweight, but they can be difficult to machine. Challenges include tool wear, delamination, and achieving a smooth finish. Specialized tools and techniques are often needed.
How does the choice of material affect the surface finish of a machined part?
The properties of a material, like hardness and ductility, affect the surface finish we can achieve. Softer materials often result in smoother finishes, while harder materials might need extra finishing steps to reach the desired quality.
What is the significant of material availability in CNC machining?
The availability of materials impacts lead times and production schedules. Opting for materials that are easy to source can minimize delays and ensure timely delivery of machined parts. It's crucial to consider the supply chain and material availability when planning production.
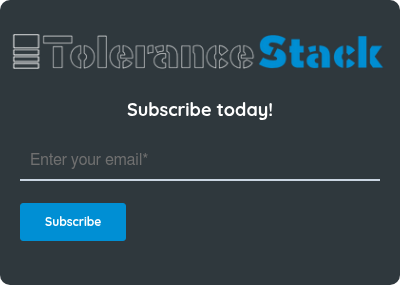
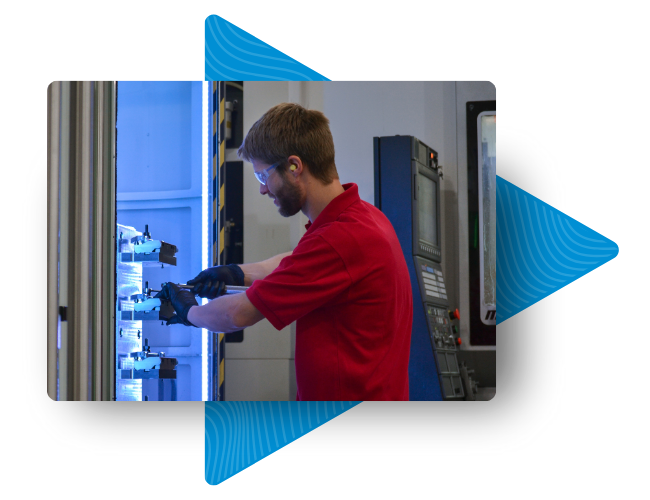
Let's connect
Want to learn more about our CNC machining services? Schedule a time to speak with our team.