Machining Cost
This article explains the key factors affecting CNC machining costs and how to optimize your project for maximum efficiency and cost effectiveness.
Table of Contents
Overview | Design | Fixed Factors | Scaled Factors | Unit Cost | FAQ
Overview
In CNC machining, costs vary for each project. Things like design, equipment, materials, and inspection needs all factor into the price tag.
Countless factors influence machining cost, but the main culprits are the following:
- Part design
- Material
- NRE and programming
- Machining process
- Tooling
- Post-processing
- Volume
Design
The design and shape of a part greatly influence the cost of CNC machining.
The more complex a part is, the higher the manufacturing cost. Complex parts often need advanced machinery, more machining time, multiple setups, additional resources, and thorough inspections -- all of which increase costs.
Certain design features can also increase costs. These include:
- Sharp internal corners
- Thin walls
- Deep cavities
- Non-standard hole sizes
- Lettering
Such features should be avoided unless necessary. Additionally, design specifications like surface roughness or tolerancing may need multiple passes and inspections, further raising costs.
Large parts cost more to produce because they need more raw materials, resources, and manufacturing time and effort.
Fixed Cost Factors
Fixed costs represent the foundational expenses incurred at the start of a CNC machining project; these costs primarily include setup and programming. Regardless of the quantity of parts ordered, these costs are amortized across the entire production run.
This means that as the number of machined parts increases, the fixed cost per unit decreases, offering greater cost efficiency and value for larger orders. Understanding this distribution can help businesses optimize their budgets and make informed decisions about production volumes.
Programming and NRE
Programming and non-recurring engineering activities for machining jobs incur a significant one-time cost. For complex prototype parts, this can make up a large part of the total job cost. Further, the more complex features lead to more complex programming. Aim for the simplest machining strategy and workholding setups that use standard tools whenever possible.
Setup
Job setup is the process of preparing the machine and the workpiece for the machining operation, and is a fixed cost spread over the total number of parts produced. To lower these costs, follow DFM guidance similar to reducing programming expenses. Designing for simple or standard setups helps cut job setup costs in both prototypes and production.
Scaled Cost Factors
Unlike their fixed counterparts, scaled cost factors correspond directly to order volume. If you place a high volume order, you'll naturally spend more on these things compared to a low volume run.
Material
The material used to make a part is a key factor in its cost. There are various costs linked to machining a material, with the primary one being the material's own cost. Material prices vary based on their availability, desirable properties, and production costs.
Besides material costs, machinability significantly affects expenses. Materials that are difficult to machine require more time and effort, and in CNC machining, time equates to money. The longer it takes to machine a part, the higher the cost. Additionally, challenging materials use more resources, such as cutting fluids, electricity, and tools.
Related Read: What to Consider when Calculating Material Cost ➡️
Machining Process
The chosen machining process is another key cost driver that you should keep in mind when approaching a CNC machining project. Costs related to a machining process include:
- Machine type and capabilities (i.e., 3-axis mill vs. 5-axis mill-turn machine)
- Machine time (i.e., spindle time, setup time, changeover time)
- Labor costs (i.e., required programming, setup, and operator costs; location has an impact here, as well)
Tooling
Cutting tools also influence total equipment cost and scale accordingly with the volume of your order. Material, coating, and geometry all affect tooling cost, and costs are further extrapolated based on tool wear and/or breakage. For example, cemented carbide tools, which are harder, more heat resistant, and able to withstand extreme speeds, cost over two times more than tool steel tools.
Post-Processes
Some applications need additional steps like heat treatment, surface finishing, and coating to enhance their performance, features, and appearance after the machining operation. These extra processes add to the part's cost, and obviously those costs correspond to order volume.
Cost per Unit
Taking part design, as well as fixed and scaled factors. into account, keep in mind that there is an inverse relationship between per-unit cost and production volume, often referred to as economies of scale.
While overall costs may be lower for low-volume production, they will have a higher per-unit cost. Concurrently, there are more upfront costs associated with high-volume production, but the per-unit cost is much lower.
Let’s take a closer look at the relationship between production volume and cost.
Low Volume Production
Low-volume production is an essential and often necessary phase in the manufacturing process and product lifecycle. Low-volume production requires minimal initial investment and is ideal for testing a product's viability before moving to large-scale production. However, optimizing these processes can be challenging since the cost benefits of mass production are not yet applicable.
Small order quantities often come with higher costs, and many CNC machining suppliers have minimum order requirements that might be more than you need for low-volume production.
High Volume Production
As you increase the number of identical parts produced, the cost per unit drops significantly. This cost reduction happens because you only need to handle the CAD design, CAM preparation, and machine set-up once for all parts.
Generally, ordering in larger quantities leads to cost savings throughout the supply chain. This includes savings on raw materials, castings, machined parts, post-processing, and more.
The unit price decreases significantly as production volume increases. For example, increasing production from one to five units can halve the unit price. Ordering in very large quantities, such as over 1,000 parts, can reduce the unit price by five to ten times. A simple way to reduce cost is to take advantage of these economies of scale by ordering higher quantities.
You should also aim to keep your part simple. You pay extra for complexity in the world of CNC machining, and geometries that need specialized tooling, custom fixtures, or multiple setups will incur additional costs accordingly.
Frequently Asked Questions
What are the main factors that influence the cost of CNC machining?
Key factors affecting the cost of producing a part include the choice of materials, the complexity of the part, machining time, tool wear, labor expenses, and post-processing needs.
How does material selection affect machining cost?
Choosing the right material affects costs because of variations in price, ease of machining, and availability. Harder or rare materials might need special tools and take longer to machine, which raises costs.
Why does part complexity influence machining cost?
Complex parts need more machining steps, longer setup, and detailed programming, which increases time, labor, and costs.
How does machining time affect the cost of a part?
Longer machining times increase costs due to more machine hours needed. Using efficient machining strategies can lower both time and costs.
What role does tool wear play in machining cost?
Tool wear increases costs by requiring more frequent tool changes and replacements. It can also result in lower-quality parts and higher scrap rates, further raising expenses.
How do labor costs influence CNC machining expenses?
Labor costs cover the wages of machine operators, programmers, and quality control staff. Skilled workers are crucial for top-notch machining, but they also increase the total cost.
What is the impact of post-processing on machining cost?
Post-processing steps like deburring, polishing, anodizing, and coating can increase costs. However, they are often essential to achieve the required surface finish and part quality.
How does batch size affect the cost of CNC machining?
Producing larger batches can lower the cost per part. This is because setup costs are divided among more parts, and buying materials in bulk can be cheaper.
What is the significance of machine maintenance in controlling machining costs?
Regular machine maintenance keeps performance high, minimizes downtime, and avoids expensive repairs. Properly maintained machines deliver better-quality parts and work more efficiently, lowering overall costs.
How can design optimization help reduce machining costs?
To optimize design, simplify part shapes, minimize machining steps, and choose affordable materials. Working with engineers and machinists early in the design process can save costs significantly.
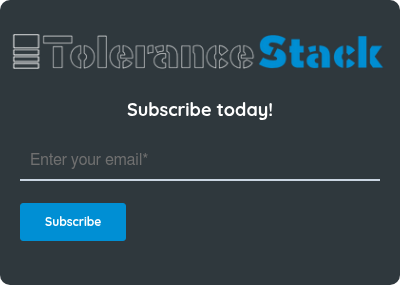
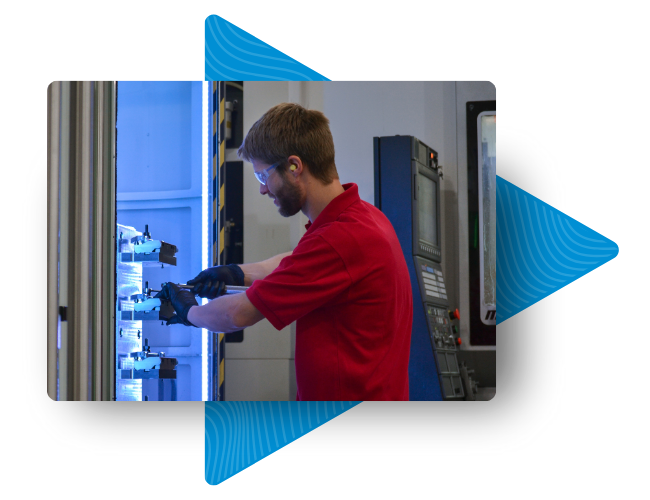
Let's connect
Want to learn more about our CNC machining services? Schedule a time to speak with our team.