CNC Turning
This article covers CNC turning, detailing its process, benefits, limitations, and essential information for making parts.
Table of Contents
Overview | Machine Anatomy | Types | Tools | Operations | FAQ
Overview
CNC turning is a machining process where a lathe is used to rotate the metal while a cutting tool moves in a linear motion to remove metal along the diameter, creating a cylindrical shape. The cutting tool can be angled differently to create different forms.
Unlike working on a mill, the cutting tool is positioned against the workpiece, which is rotated by the spindle.
Turning produces rotational, typically axi-symmetric, parts with many features, such as holes, grooves, threads, tapers, various diameter steps, and even contoured surfaces.
CNC turning boasts several noteworthy advantages, including:
Cost and Volume
CNC lathes offer the lowest cost per part compared to all other CNC machining operations. They’re also capable of very high volume production runs, making them an ideal machining process for manufacturers who want to reduce costs once they progress past the prototype phase.
Tolerances
Turning can create parts with extremely high tolerances. Because of the high tolerances and surface finishes that turning can offer, the process is often used to add precision rotational features to a part whose basic shape has already been formed through a different method.
Labor Requirements
Turning does not require a highly skilled operator of the machine. To handle a CNC lathe, a machinist can complete a set amount of coursework and earn certification from an accredited industrial training organization.
Due to the nature of CNC turning, only rotatable parts can be used on the machines. This can limit you as far as what types of components you can subject to turning or force you to rely on additional procedures and machines.
Anatomy of a CNC Lathe
Headstock
The lathe headstock powers the machine, holding and centering the workpiece. Its size determines the lathe's "swing," or the largest diameter workpiece it can handle. A larger swing can be beneficial for certain tasks.
The motor's power limits work capacity by driving the spindle and rotating the workpiece. The headstock's main bearings handle heavy loads and vibrations, making them crucial for maintenance, especially in frequently used machines.
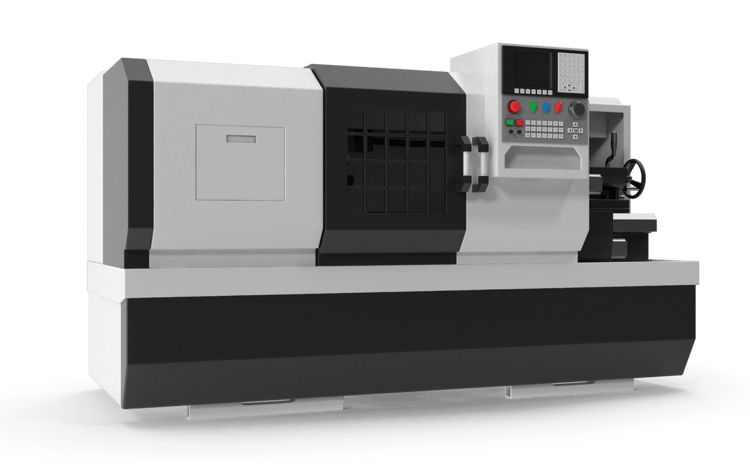
Tailstock
The tailstock of a lathe is essential for various tasks. Positioned opposite the headstock, it secures the workpiece's end, providing support against heavy loads. It can also hold a drill bit for drilling along the workpiece's axis. Typically, it features a Morse taper tool holder in a precision feed for strong longitudinal control.
Tailstock functions include a centering tool to support lateral forces prevents long workpieces from bending away from the cutter, a drill chuck for small twist drills, allowing precise drilling into the workpiece's center at an exact depth, and a larger drill bit with a Morse taper shank to drill directly into the end of the workpiece.
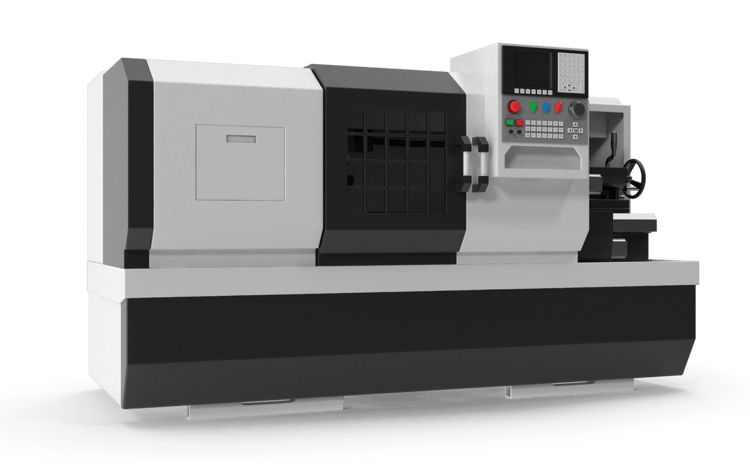
Tailstock Quill
The quill of the tailstock holds the Morse taper. It is a cylindrical mount that lets you attach chucks, drills, and more to the tailstock. The quill moves towards the workpiece for drilling or stabilizing.
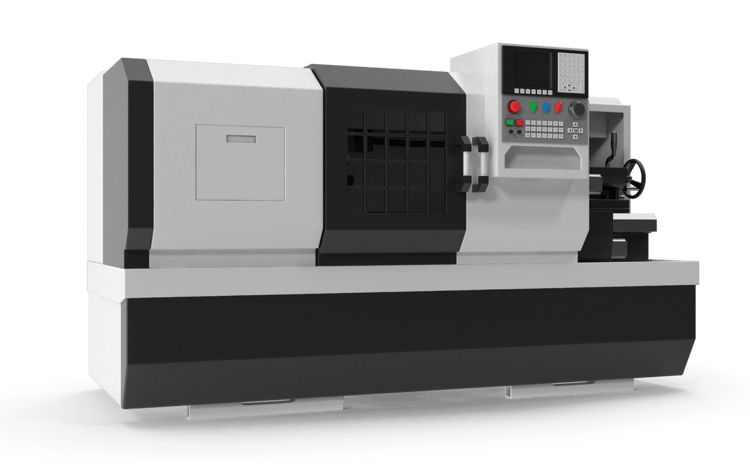
Tool Turret
The tool turret is the working end of the CNC lathe. Different tools are positioned for operation, and their cutting edges are accurately recorded in the machine setup. Each tool can be rotated into the cutting position one at a time. Unlike manual lathes, this process is automated, allowing for automatic tool selection and positioning.
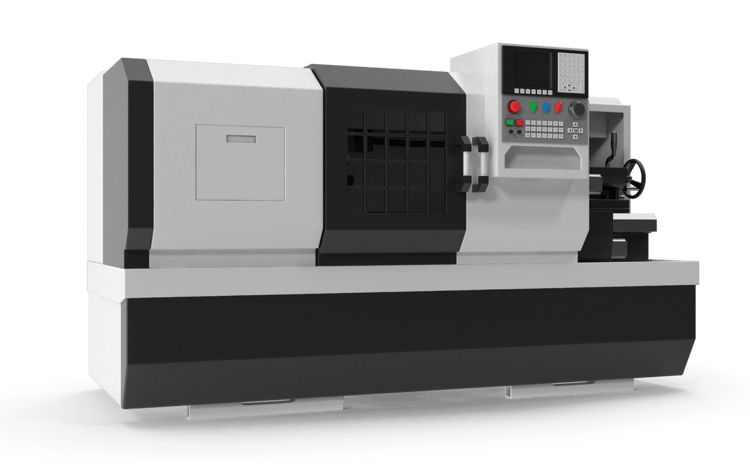
Lathe Bed
The lathe bed is the main structure that holds the machine together. It is typically a long beam that supports all the working parts. The bed must be strong enough to avoid any distortion, even under heavy use.
The best lathe beds can naturally reduce vibrations. Those with high hysteresis effects can convert vibrational energy into heat. To test for hysteresis, you can hit the material with a hammer—a dull "thud" means high hysteresis, while a sharp "ding" is not ideal. CNC lathe beds are typically made from cast iron, mild steel, ductile cast iron, or Granitan, an artificial stone substitute. Granitan offers low risk of cracking and chipping, enhanced toughness, and excellent vibration damping.
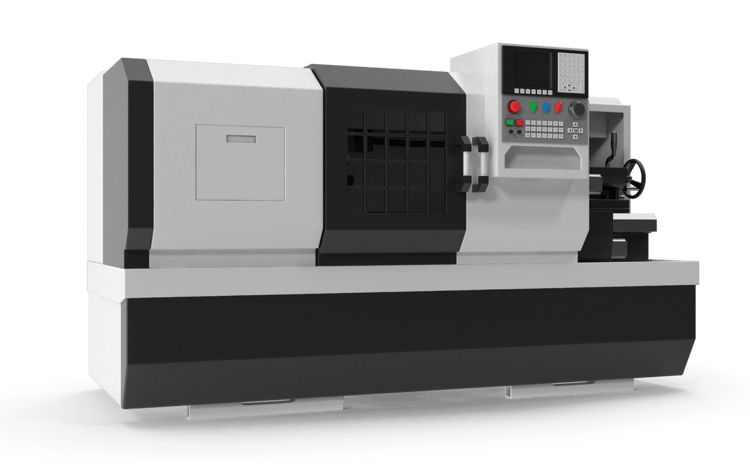
Chuck
The chuck is a vital part of a lathe. It holds the workpiece in place at the center, making it easy to load and unload. While it connects to the headstock, it is not a part of it.
CNC lathes use different types of chucks, such as the three-jaw (universal), four-jaw, combination, magnetic, collet, and drill and pin chucks.
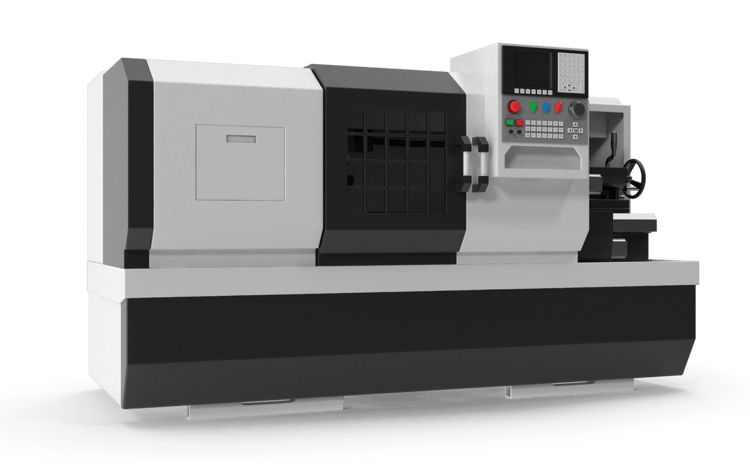
Foot Pedals
Foot switches, or pedals, let operators control machine setup or unloading while keeping their hands free. These pedals manage tasks like opening or closing the chuck (if it's hydraulic or pneumatic), positioning the tailstock for centering and support, and serving as an emergency stop to prevent errors or accidents.
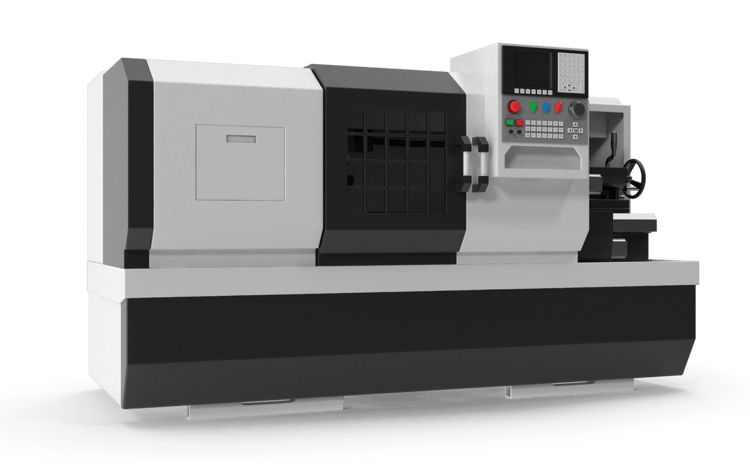
Control Panels
A CNC lathe has two main control parts: the machine panel and the control panel. The machine panel lets the operator adjust the tool's settings and cutter position, and it is used to make small manual adjustments to the machine's axes. The control panel is for entering and editing programs, which are shown on the screen as G-code.
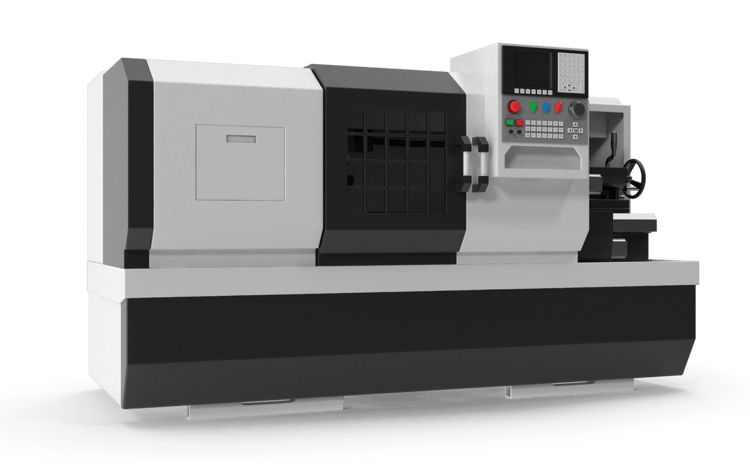
Types of Turning Machines
CNC turning machines come in two main types: vertical and horizontal. Additionally, it's crucial to understand the distinction between a CNC lathe and a CNC turning center.
A CNC turning center can perform various operations, whereas a lathe is specifically for turning. A lathe cuts a rotating workpiece, and turning is the general term for this rotational cutting process.
Turning centers are versatile machines with multiple functions and axes. They can include a C-axis, Y-axis, and driven tools on the turret, allowing them to perform not only turning but also milling, drilling, and tapping operations.
A vertical turning center combines features of both a turning center and a vertical lathe. It is ideal for machining shorter components that do not need a sub-spindle, tailstock, or bottom turret, helping to minimize the machine's footprint.
Horizontal Lathe
In CNC turning, a horizontal lathe is the most commonly used lathe and, as the name implies, features a spindle set horizontally.
A horizontal spindle allows the workpiece to be placed between the headstock and tailstock.
Horizontal lathes are adaptable and can manage various sizes and shapes of workpieces.
The horizontal setup simplifies loading and unloading workpieces and conducting different machining tasks.
Well suited for producing shafts, rods, tubes, and other cylindrical parts.
Vertica Lathe
As its name hints at, vertical lathes have a spindle that is set vertically.
This makes it easier to manage larger and heavier workpieces and manage chip removal more effectively since gravity helps clear the work area.
The workpiece is placed on a rotating table that can hold large and heavy items.
The design offers greater stability for machining large parts, minimizing deflection and vibration risks.
Well-suited for producing large-diameter components like wheels, gears, and large bearings.
Swiss Lathe
A Swiss lathe is a specialized lathe that's used for machining small, cylindrical components.
The workpiece moves along the Z-axis while the cutting tools remain stationary, improving precision and stability.
A guide bushing stabilizes the workpiece, enhancing accuracy by minimizing deflection and vibration.
Swiss lathes have several tool stations for quicker and simultaneous machining.
Well-suited for producing screws, pin, and other small components with complex geometries.
Turning Tools
The tools handle all the cutting tasks. They are usually placed in a tool holder and inserted into the spindle as needed. Various tools are required to create a complete part, as there is no universal solution in manufacturing. Below are the most commonly used tools in a standard machining setup.
An OD rougher is a tool used for roughing operations on the outer diameter (OD) of a workpiece.
An OD finisher refers to a tool used for finishing operations on the outer diameter (OD) of a workpiece.
An OD groover is a specialized tool used for creating grooves on the outer diameter (OD) of a cylindrical workpiece.
A face groover is a specialty tool that’s used for creating grooves on the face of a workpiece.
A threader is a specialized tool used for cutting threads on the outer or inner surfaces of a cylindrical workpiece.
Drills are used to create holes in workpieces, while taps are used to cut internal threads in a pre-drilled hole.
ID groovers are used to create grooves on the inner diameter (ID) of a cylindrical workpiece.
An ID boring bar is a specialty tool that’s used to enlarge and finish the inner diameter of a cylindrical part.
Turning Operations
The turning process uses a lathe machine to move the cutting tool in a straight line along the rotating workpiece. This removes material around the edge until the desired diameter is reached, allowing for the creation of cylindrical parts with features like slots, tapers, and threads.
Turning involves using single-point cutting tools to shape the rotating workpiece. These tools are designed for specific tasks such as roughing, finishing, facing, threading, parting, forming, undercutting, and grooving.
Straight Turning
Straight turning, also called cylindrical turning, reduces the workpiece diameter evenly to ensure consistency. It is typically a "roughing" process that removes large amounts of material before precision cutting.
Facing
Facing, or face turning, is a method to create a flat surface at a right angle to the workpiece's rotation. The tool is secured in a holder on the lathe's carriage. It moves across the part's rotational axis. Face turning can be done as an initial rough cut or a final finishing cut.
Drilling
Drilling can be performed using a lathe or a turning center. Advanced turning centers allow drilling in various orientations, not just along the central axis.
Boring
Boring is used after drilling to make a hole larger. The tool enters the existing hole and removes material from its inner wall.
Taper Turning
Taper turning creates a cylinder with a diameter that gradually decreases.
Grooving
Grooving is done when a shaped tool is pressed into the component gouge to form a narrow cavity. Grooving is typically used to create features like O-ring or circlip grooves and contouring operations. A grooving tool is sometimes also called a parting-off tool and is used to remove the completed part from the workpiece stock.
Parting
Parting involves cutting deeply into the material to separate the finished piece from the original stock.
Knurling
Knurling creates a diamond pattern on the outer surface of a part by compressing the material, not cutting it. This technique is primarily used to enhance grip on parts, especially those requiring extra traction.
Threading
Threading involves creating grooves in a hole or on the outer surface of a workpiece, allowing it to be screwed into other objects.
What is CNC turning?
CNC turning is a process where computer-controlled machines spin a workpiece against a cutting tool to precisely shape cylindrical parts.
What materials can be used in CNC turning?
CNC turning can be done on various materials, including metals like aluminum, steel, and brass, as well as plastics and composites.
What are the advantages of CNC turning?
The benefits include precise accuracy, consistent results, the ability to craft intricate designs, and versatility with different materials. It also minimizes manual work, boosting efficiency.
What industries use CNC turning?
CNC turning is crucial in industries like aerospace, automotive, medical, electronics, and manufacturing for creating precise and high-quality parts.
What is the difference between CNC turning and milling?
CNC turning rotates the workpiece while the cutting tool stays still, whereas CNC milling uses rotating tools to cut material from a stationary workpiece.
How does CNC turning achieve high accuracy?
We achieve high accuracy with advanced CNC machines, precise tools, and careful programming. These machines can make small adjustments to maintain tight tolerances.
What are common challenges in CNC turning?
Key challenges include tool wear, material characteristics, thermal expansion, and maintaining precise tolerances. Regular machine upkeep and strategic planning can effectively address these issues.
What is the role of CAD/CAM software in CNC turning?
CAD and CAM software are essential for designing parts and creating CNC machine toolpaths, ensuring precise and efficient turning processes.
How do you select the right cutting tools for CNC turning?
Choosing the right cutting tools depends on the material, the desired finish, and the part's complexity. We consider factors like tool material, shape, and coating.
What is the importance of cutting fluids in CNC turning?
Coolant and other cutting fluids reduce heat during turning, preventing tool wear and preserving the workpiece's quality. They also help remove chips and enhance the surface finish.
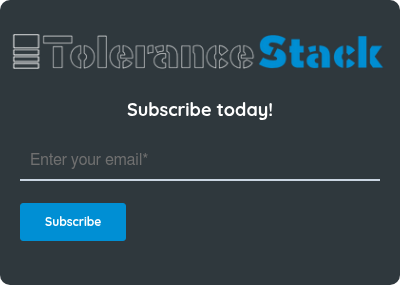
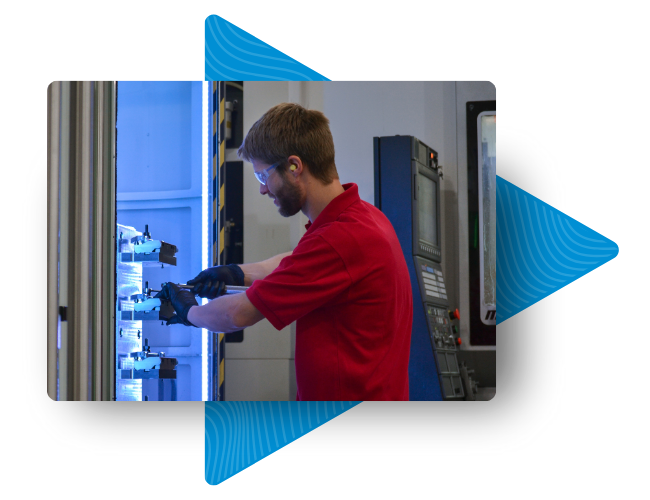
Let's connect
Want to learn more about our CNC machining services? Schedule a time to speak with our team.