CNC Milling
This article covers CNC milling, detailing its process, benefits, limitations, and essential information for making parts.
Table of Contents
Overview | Machine Anatomy | Types | Tools | Operations | FAQs
Overview
CNC milling is a machining process where the cutting tool in CNC milling rotates and moves around a stationary workpiece to shape a part. Milling machines are known for their high precision and tight tolerances.
Unlike turning, which works only with cylindrical parts, milling can create a wide range of shapes and contours in materials that are challenging or even impossible to machine with other methods.
CNC milling offers a number of key benefits, including:
Scalability
CNC milling is versatile for any production size, from custom projects to mass production. Its repeatability and speed make it ideal for prototyping and high volume production, reducing costs as production volume increases.
Tolerances
CNC milling achieves exceptional precision, with tolerances as tight as 0.025 mm. This level of accuracy is essential for industries such as aerospace, automotive, and medical devices.
Variability
CNC milling can precisely create various features such as pockets, threads, chamfers, slots, and cavities, in addition to producing different shapes.
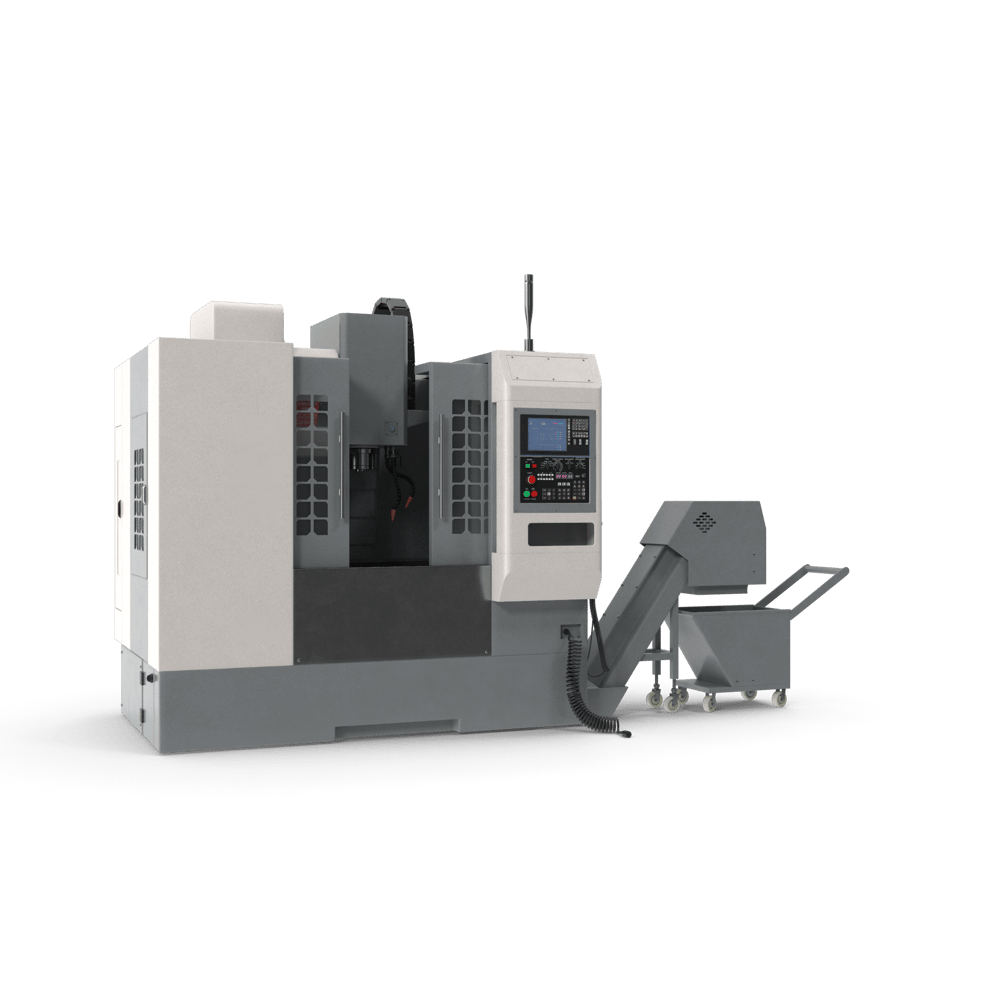
Anatomy of a CNC Mill
Spindle
The spindle holds the cutting tool in place
Control panel
This is where the computer interface is located and how the operator controls the machine
Column
The Column is the main frame and support of the machine; it holds other components in place
Saddle
The saddle is attached to the column of the machine; it supports the worktable
Worktable
The worktable is located on top of the saddle; it is where the operator places the workpiece and uses a workholding device
Base
The base is what provides support for the whole machine on the ground
Types of Milling Machines
The range of milling machines is vast, including types like planer, gantry, turret, and bed. Broadly, CNC milling machines are categorized into two main types: vertical machining centers (VMCs) and horizontal machining centers (HMCs).
In VMCs, the spindle stays fixed while the table moves beneath it. Sometimes, the table moves up to the spindle, or the spindle moves along the Z-axis. These machines are very sturdy, allowing for precise component production. However, they have a smaller work area. VMCs can operate with 3 axes (X, Y, Z), 4 axes (X, Y, Z, A), or even 5 axes (X, Y, Z, A, B).
In HMCs, the spindle is positioned horizontally. These machines are perfect for long production runs because they can handle up to three times more work than a VMC, as long as there is enough work to keep them running. However, HMCs are more costly than VMCs. They allow for continuous production since a block of material can be set up on the machine bed while another part is being made. The spindle can quickly switch to the next ready block, making changeovers fast.
3-Axis Mill
In 3-axis CNC milling machines, the cutting tool or workpiece can move in three directions: X-axis (left and right), Y-axis (forward and backward), and Z-axis (up and down). To access specific areas, the workpiece needs to be manually repositioned.
Pros | Cons |
|
|
5-Axis Mill
5-axis mills have two more rotary axes than 3-axis ones, giving the cutting tool access to more areas through additional movements of the workpiece. 5-axis mills come in two types: indexed, where the tool pauses as the workpiece rotates, and continuous, where both rotate simultaneously without stopping.
Pros | Cons |
|
|
Milling Tools
The tools handle all the cutting tasks. They are usually placed in a tool holder and inserted into the spindle as needed. Various tools are required to create a complete part, as manufacturing does not follow a "one size fits all" method. Below are the most commonly used tools in a standard machining setup.
End Mill
An end mill is a versatile tool that cuts in three directions and comes in styles like flat, corner radius, roughing, ball, and taper. It is defined by its flutes, helix angles, base, and coating materials.
Face Mill
A face mill is crafted to cut large surface areas, known as facing. Its cutting edges are on the tool's perimeter, and the teeth are typically made of carbide inserts.
Thread Mill
A thread mill creates threads by rotating around the shank in a helical pattern to cut the thread shape.
Slotting Cutter
These cutters are designed to create t-slots along a part's length. Due to their shape, they must enter and exit from an open side of the material.
Milling Operations
While many milling operations are straightforward, it's beneficial to explore them in greater detail.
Face Milling
Face milling is highly valued in manufacturing for creating precise and smooth surfaces, even on large pieces. It can form pockets and steps in metal by flattening and smoothing the top. A face mill has cutting edges on its disk-like face, which shave off material horizontally from a workpiece until the preset depth is reached.
Slot Milling
Slot milling uses a slot cutter, similar to a circular saw blade, to create slots like grooves or trenches. This tool cuts into the sides of materials, while an end mill can also cut on its side and face. It essentially carves channels in the material, such as keyways and other grooves.
End Milling
The end milling tool has cutting edges on its end and sides, enabling it to create slots, pockets, and contours. This versatile tool is popular because it can cut straight down like a drill bit and also move sideways.
Thread Milling
Thread milling creates the spiral threads on screws and bolts. This tool, with its multiple cutting edges, can make threads in different materials and sizes, even for complex designs. It rotates around the material, following the thread path to cut the threads. While its main job is to create threads, it performs this task exceptionally well.
Shoulder Milling
Shoulder milling uses tools like end mills to cut material from the side of a workpiece, forming flat, 90-degree angles similar to steps.
Side Milling
Side milling uses a cutter or end mill to shave off thin layers from the side of a workpiece, making it perfect for crafting flat or shaped surfaces.
Profile Milling
Profile milling is ideal for creating complex shapes and surfaces, using CNC machines with tools that have multiple cutting edges and a ball tip for smoothing. It's perfect for making intricate parts like dies and molds.
Gear Milling
This milling technique is tailored for making gears and gear teeth, such as those found in car engines or clocks. It employs gear hobbing or milling cutters to shape the gear teeth by removing material. While simple gears can be crafted with manual machines, CNC machines are generally used for more intricate gears.
Angle Milling
Angle milling shapes parts with beveled edges and angles. It uses special tools like cone-shaped or flat cutters that can be tilted to the needed angle. This tilt is achieved with a tilting arbor or a machine with four or more axes.
Form Milling
Form milling creates detailed and contoured shapes on surfaces using either specialized cutters that match the desired shape or standard cutting tools. This process is frequently employed in the automotive, aerospace, and mold-making industries, often utilizing CNC machines.
Straddle Milling
Straddle milling uses two milling cutters placed side by side on an arbor to create parallel slots, grooves, or surfaces on a material. This dual-cutter setup allows for faster completion, effectively cutting the time in half. It is commonly used for keyway milling and machining flat surfaces on opposite sides of a shaft.
Plain Milling
Plain milling may not have an exciting name, but it is an essential manufacturing technique. It involves using a flat, horizontal cutting tool to remove material from a surface, creating square or rectangular features.
What is CNC milling?
Precision CNC milling is a process where computer-guided machines precisely cut material from a workpiece. This method is ideal for making intricate parts with exact specifications.
What materials can be used in CNC milling?
Precision CNC milling can be done on various materials, including metals like aluminum, steel, and titanium, as well as plastics and composites.
What are the advantages of CNC milling?
The benefits include precise accuracy, consistent results, the ability to craft intricate designs, and versatility with different materials. It also minimizes manual work, boosting efficiency.
What industries use CNC milling?
CNC milling is crucial in industries like aerospace, automotive, medical, electronics, and manufacturing for creating parts with high precision and quality.
What is the difference between CNC milling and turning?
CNC milling uses rotating tools to cut material from a fixed workpiece, while CNC turning rotates the workpiece against a fixed tool.
How does CNC milling achieve high accuracy?
We achieve high accuracy with advanced CNC machines, precise tools, and careful programming. These machines can make small adjustments to maintain tight tolerances.
What are common challenges in CNC milling?
Key challenges include tool wear, material characteristics, thermal expansion, and maintaining precise tolerances. Regular machine upkeep and strategic planning can effectively address these issues.
What is the role of CAD/CAM software in CNC milling?
CAD (Computer-Aided Design) and CAM (Computer-Aided Manufacturing) software are essential for designing parts and creating toolpaths for CNC machines. They ensure the milling process is accurate and efficient.
How do you select the right cutting tools for CNC milling?
Choosing the right cutting tools depends on the material, the desired finish, and the part's complexity. We consider factors like tool material, shape, and coating.
What is the importance of cutting fluids in CNC milling?
Cutting fluids, or coolants, reduce heat during milling, preventing tool wear and preserving the workpiece. They also help remove chips and enhance the surface finish.
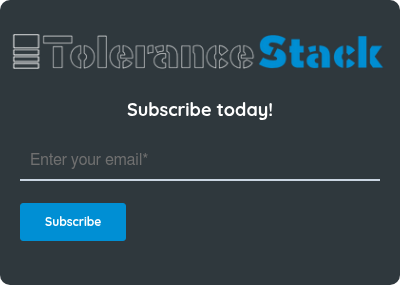
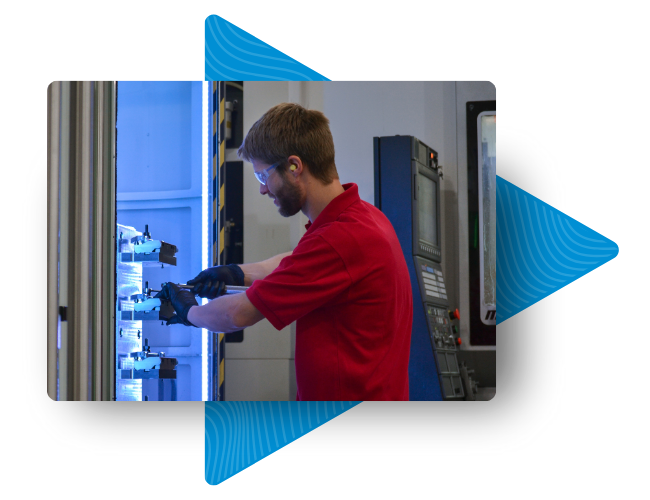
Let's connect
Want to learn more about our CNC machining services? Schedule a time to speak with our team.