Design for Manufacturability
This article explores the design for manufacturability (DFM) process, with a focus on CNC machining.
Table of Contents
Overview
Design for manufacturability (DFM) is an engineering approach that focuses on design first, making the final product more efficient and cost-effective to produce.
Focusing on DFM during the prototype stage helps engineers design, refine, and perfect a part before it enters production. This approach cuts costs, shortens lead times, and enhances the quality of custom parts. It involves reducing the number of parts in the final product, standardizing parts for uniformity, creating modular designs for future use, and streamlining the manufacturing process.
A successful DFM analysis ensures your design is ready for production, leading to lower costs and higher efficiency while maintaining the quality of your parts and products.
For optimal results, involve key stakeholders early in the project. This includes manufacturers, who will transform the engineer's design from a CAD file or prototype into a consistent, compliant, and cost-effective product.
DFM Process for CNC Machining
The DFM process works by examining five key principles: process, design, material, environment and compliance, and testing.
Process
Selecting the right manufacturing process is key to effective DFM. The process you choose impacts cost, lead time, and part quality. Aligning your design with process capabilities avoids extra steps and unnecessary costs—ensuring efficient, consistent manufacturing.
Design
After selecting a manufacturing process, start designing the part. Pay attention to key factors like wall thickness, surface details, texture, and transitions specific to your chosen process. DFM follows the principle of "the simpler, the better." While not every design can be simple, more complex designs are riskier to produce. They might fail during manufacturing or lead to significantly higher costs.
Material
When choosing the right material for your project, consider the specific properties your part needs, such as heat resistance, water resistance, strength, and flexibility. These properties will depend on how the final part will be used.
Related Read: Material Selection Strategy for Machined Components
Environment
Environmental factors significantly influence your part's design. Will it face high stress or force in an industrial setting, or will it be used in an office? Consider where and how the part will be used. This DFM principle ensures your part performs well in its intended environment throughout its lifespan.
Compliance and Testing
In many cases, your part must meet specific industry, internal, or third-party standards. For instance, if your components are used around food, they must comply with all food safety regulations. Consider all relevant standards and plan for testing to ensure compliance during the DFM process.
A successful DFM analysis reduces costs while maintaining or even enhancing the performance of a part or product. Besides the five main principles, other factors also influence the DFM process:
- Volume – producing fewer parts can lead to higher start-up costs, resulting in increased unit prices. However, as you produce more units, the unit price decreases
- Product Complexity – DFM focuses on simplifying designs. Complex designs increase the risk of expensive or inefficient production
- Material Availability – lead time, cost, and other procurement factors impact the whole DFM process
- Appearance – incorporating surface finishes, colors, custom markings, and other aesthetic features increases production costs and time. It's advisable to consider these cosmetic aspects during the design phase, well before production begins
DFM Guidelines by Common Features
Each use case is unique, making it challenging to list best practices for every situation. However, here are some dependable guidelines for designing common CNC machined features.
Profiles
Avoid designing profiles with sharp internal corners. CNC tools like end mills are cylindrical and can't create sharp corners. Instead, use fillets or radii to match the tool's shape. This reduces stress and makes the part easier to machine. Also, keep wall thickness consistent to prevent warping and ensure accurate material removal for better precision.
Design profiles for easy tool access. Hard-to-reach features can increase machining time and require costly specialized tools. Align features with the CNC machine's main axes to simplify machining and boost efficiency. Avoid deep cavities and narrow slots to prevent tool deflection and achieve a smoother surface finish.
Pockets
Pockets and cavities are indented areas in a part that help reduce weight, make room for other components, or meet specific design needs. By applying DFM principles, engineers can cut down on machining time, save materials, and enhance the final product's quality.
To ensure optimal performance, keep the depth of pockets and cavities no more than four times their width. This prevents tool deflection and improves surface finish. Avoiding deep cavities reduces tool breakage risk and enhances machining stability. Maintaining consistent wall thickness prevents warping and ensures even material removal.
Design pockets and cavities for easy tool access to save time and reduce costs. Hard-to-reach features can increase machining time and require expensive specialized tools. Align features with the CNC machine's main axes to streamline the process and boost efficiency. Use rounded internal corners instead of sharp ones to fit tool shapes and minimize stress.
Fillets
Fillets are rounded edges or corners that help reduce stress and increase the strength and durability of a part. By adding fillets to a design, engineers can improve the component's performance and lifespan. It's important to match fillets with the tool shape used in CNC machining. Most CNC tools are cylindrical, so internal corners will naturally have a radius. Designers should choose fillets that fit the tool's radius to prevent sharp corners, which can cause stress and potential failure. Keeping fillet sizes consistent throughout the part also ensures even material removal and better dimensional accuracy.
Designing fillets for easy tool access is crucial. Hard-to-reach features can increase machining time and require special tools, raising costs. Aligning fillets with the CNC machine's main axes simplifies machining and boosts efficiency. Adding fillets in high-stress areas also improves part durability and performance.
Chamfers
Chamfers are angled cuts on part edges that remove sharpness, aid assembly, and meet design needs. Adding chamfers improves a component's performance and lifespan.
Ensure chamfers have the right angles and sizes to match CNC machining tools, which use angled cutters. This prevents sharp edges that can cause stress and failure. Keeping chamfer sizes consistent across the part ensures even material removal and better accuracy.
Design chamfers for easy tool access to reduce machining time and avoid costly specialized tools. Align chamfers with the CNC machine's main axes to streamline the process and boost efficiency. Adding chamfers in high-stress areas enhances part durability and performance.
Bosses
Bosses are raised cylindrical features used for mounting, alignment, or adding material for threads. By applying DFM principles, engineers can improve these features' functionality and manufacturability, resulting in cost-effective and reliable parts.
A key guideline is to design bosses with the right size and tolerances. They should be wide enough to provide the needed strength and support. Keeping boss heights consistent helps with even material removal and better accuracy. Avoid sharp edges on bosses, as they can cause stress and failure. Instead, use fillets or chamfers at the base to spread stress evenly.
Design bosses for easy tool access to reduce machining time and avoid costly specialized tools. Align bosses with the CNC machine's main axes to streamline the process and boost efficiency. Keep bosses away from part edges to prevent tool deflection and achieve a smoother surface finish.
Slots
Slots are long cuts that can be used to fit other parts, create paths for fluids or wires, or add structural features. By following DFM principles, engineers can save machining time, reduce material waste, and enhance the final product's quality.
To ensure optimal performance, keep the slot's depth no more than four times its width. This prevents tool deflection and enhances surface finish. Shallow slots also lower the risk of tool breakage and stabilize the machining process. Maintaining consistent wall thickness is crucial to avoid warping and ensure even material removal.
Design slots for easy tool access to reduce machining time and avoid costly specialized tools. Align slots with the CNC machine's main axes to streamline the process and boost efficiency. Use rounded internal corners instead of sharp ones to fit tool shapes and minimize stress.
Holes
Holes are essential in CNC machined parts for fasteners, alignment, or design purposes. By following DFM principles, engineers can save machining time, reduce material waste, and enhance the product's overall quality.
To ensure optimal performance, keep the hole depth no more than four times its diameter. This prevents tool deflection and improves surface finish. Avoiding deep holes also reduces tool breakage risk and enhances machining stability. Maintaining consistent wall thickness prevents warping and ensures even material removal.
Design holes for easy tool access to save time and costs. Hard-to-reach features can increase machining time and require special tools. Align holes with the CNC machine's main axes to simplify the process and boost efficiency. Use rounded internal corners instead of sharp ones to fit tool shapes and reduce stress.
Threads
Threads are essential in machined parts for fasteners, assembly, and mechanical connections. Following DFM principles helps engineers save machining time, reduce material waste, and enhance the product's overall quality.
Ensure threads are designed with the right dimensions and tolerances. They should match the tool geometry used in CNC machining, like thread mills or taps, to prevent mismatches or poor fits that can cause assembly issues or failures. Consistent thread sizes throughout the part help with uniform material removal and improve accuracy. Avoid sharp edges in thread design to prevent stress concentrations and potential failures.
Design threads for easy tool access to reduce machining time and avoid costly specialized tools. Align threads with the CNC machine's main axes to streamline the process and boost efficiency. Keep threads away from part edges to prevent tool deflection and achieve a smoother surface finish.
What is Design for Manufacturability (DFM)?
Design for Manufacturability (DFM) involves designing parts and products with the manufacturing process in mind. This approach simplifies production, cuts costs, and enhances quality by addressing manufacturing constraints during the design stage.
Why is DFM important in CNC machining?
DFM is crucial in CNC machining as it helps spot potential manufacturing issues early in the design phase. By optimizing designs for manufacturability, engineers can cut down machining time, reduce material waste, and boost overall production efficiency.
What are some key principles of DFM for CNC Machining?
Key principles of DFM for CNC machining are to simplify part shapes, reduce machining steps, choose the right materials, and design for easy fixturing and tooling.
How can simplifying part geometry improve manufacturability?
Streamlining part design makes machining easier, resulting in faster production times and reduced costs. It also lowers the chance of mistakes and ensures a more consistent final product.
What role does material selection play in DFM?
Selecting the right materials in DFM is essential because they differ in how easy they are to machine, their cost, and availability. Opting for materials that are easier to machine and more affordable can greatly enhance manufacturability.
How can designing for ease of fixturing and tooling benefit CNC machining?
Designing parts with fixturing and tooling in mind allows for secure holding and precise machining. This approach shortens setup times, boosts accuracy, and improves production efficiency.
What are common challenges in implementing DFM?
Key challenges include making sure designs are both complex and easy to produce, controlling material costs, and ensuring designs meet functional needs while being simple to manufacture.
How can collaboration between designers and machinists improve DFM?
When designers and machinists work together, they share knowledge and expertise, leading to smarter design choices. Machinists offer insights on manufacturing limits and suggest design changes to enhance manufacturability.
What is the impact of DFM on production costs?
Using DFM principles can lower production costs by streamlining designs for efficient machining, cutting down on material waste, and reducing rework. This results in cost savings and higher profitability.
How can DFM improve part quality?
DFM enhances CNC machined parts by optimizing designs for manufacturing, reducing defects, improving consistency, and boosting the product's reliability and performance.
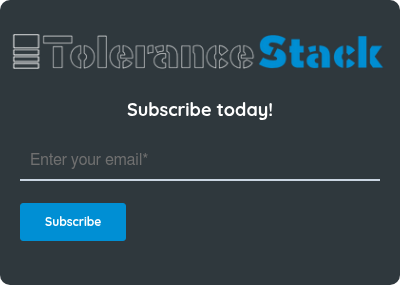
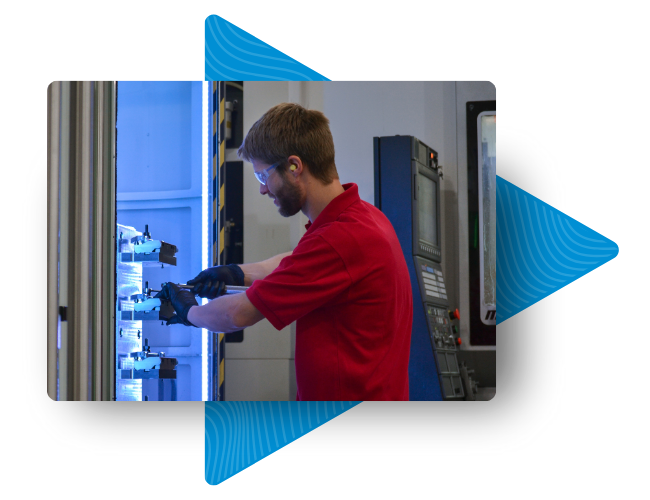
Let's connect
Want to learn more about our CNC machining services? Schedule a time to speak with our team.