Design Tips for CNC Machining
This article CNC machining design tips to optimize costs and efficiency, including features to avoid and best practices for high-quality results.
Table of Contents
Overview | Designs Tips | FAQ
Overview
CNC machining demands precision and accuracy to create high-quality designs. Therefore, following general design rules is essential for the most common features of CNC machined parts.
CNC provides significant design flexibility, but it does have some limitations. These are mainly due to the mechanics of the cutting process, particularly tool access and tool geometry.
Tool Access
The cutting tool removes material by approaching the workpiece from above. If a feature cannot be accessed this way, it cannot be CNC machined (with the exception of undercuts). Design parts for CNC machining using tools with the largest diameter and shortest length to simplify production.
Tool Geometry
Most CNC cutting tools, like end mills and drills, are cylindrical and have a limited cutting length. When material is cut away, the tool's shape is mirrored in the part. This means the internal corners of a CNC part will always have a radius, regardless of the tool's size.
To optimize your designs for CNC machining, follow a few simple steps. Adhering to design-for-manufacturing (DFM) rules allows you to fully leverage CNC machining's extensive capabilities. However, this can be challenging since there are no universal industry standards.
Designs Tips
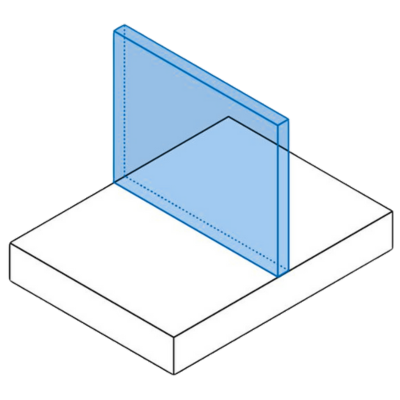
Wall Thickness
Recommended Thickness: 0.8 mm for metals, 1.5 mm for plastics
Reducing wall thickness makes the material less stiff, leading to more vibrations during machining and less accuracy. Plastics can warp due to stress and soften with heat, so it's best to use thicker walls. Always assess the recommended values individually for each case.
The minimum wall thickness is 0.8 mm for metals and 1.5 mm for plastics. For thinner walls, consider using other cost-effective methods like sheet metal fabrication.
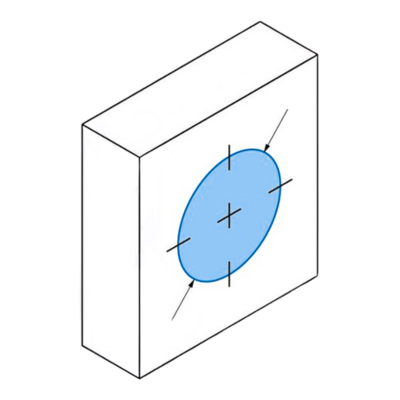
Tolerances
Recommended Tolerance: ± 0.02
Tolerances define the boundaries for an acceptable dimension. The achievable tolerances vary according to the base dimension and the geometry of the part. The values above are reasonable guidelines.
If you don't set specific tolerances, the machine will use its default settings, saving time and money. Only specify tight tolerances when necessary, and keep them consistent throughout your design to reduce machining time.
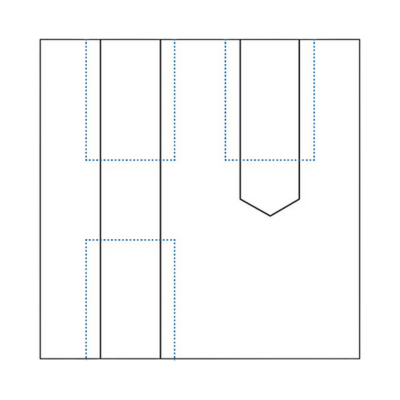
Threads
Recommended Thread Size | Recommended Thread Length |
M1 (and lower depending on the situation) | 3x nominal diameter |
Threads are created using taps for internal threads and dies for external threads, capable of cutting down to M2. CNC threading tools are widely used and favored by machinists because they reduce the risk of tap breakage and can cut threads down to M6.
Unnecessarily long threads increase machining costs. The strength of the connection does not increase when the thread length exceeds the size of the diameter by more than 1.5 times. This means that threads longer than 3x the nominal diameter are unnecessary from both a manufacturability standpoint, but also costing one.
- Threads should be no longer than 3 times the hole diameter
- For blind holes, ensure there is an unthreaded section at the bottom that is at least half the diameter of the hole
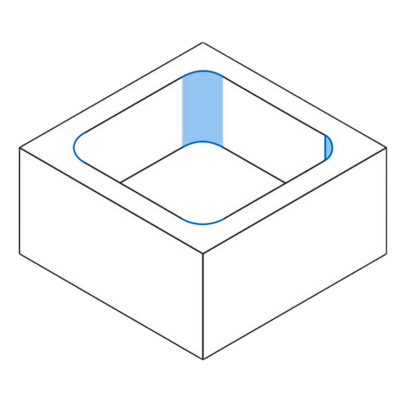
Cavities
Recommended cavity depth: 4x the cavity width
End mill tools have a limited cutting length (typically 3–4 times their diameter). Deep cavities can cause tool hanging, deflection, chip removal problems, and tool breakage. Keep cavity depths to 3-4 times their width to get good results.
For deeper cavities (6x their width), design with variable depths. You can achieve a greater diameter-to-cavity depth ratio (i.e., a maximum depth of 35 cm with a 1-inch diameter end mill); just keep in mind that specialty tooling will be required.
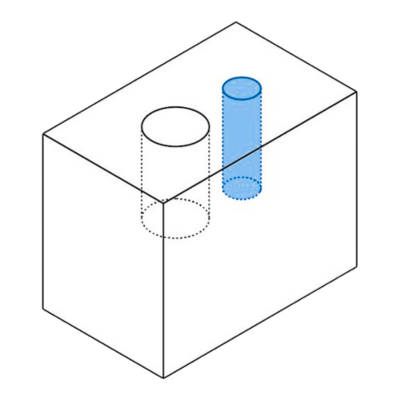
Small Features
Recommended: 2.5 mm (0.1")
Most machine shops can precisely create cavities and holes with tools as small as 2.5 mm (0.1 inches) in diameter. Features smaller than this require micro-machining, which involves specialized tools and expertise due to changes in cutting physics. It is advisable to avoid such features unless absolutely necessary.
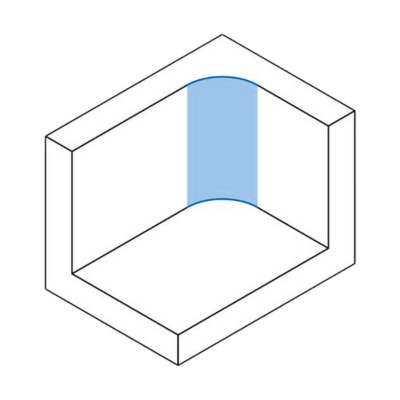
Internal Edges
Recommended Vertical Radius | Recommended Floor Radius |
⅓ x cavity depth |
0.5 mm, 1 mm, or none |
Using the recommended internal corner radii ensures the use of the right tool diameter and matches the guidelines for cavity depth.
By slightly increasing the corner radii beyond the recommended value (such as by 1 mm), the tool can cut in a circular path rather than at a 90-degree angle. This approach is preferred as it enhances the surface finish quality. If you need sharp 90-degree internal corners, consider using a T-bone undercut instead of reducing the corner radius.
End mill tools feature a flat or slightly rounded bottom edge. For different floor radii, ball end tools are used. Following the recommended values is a best practice, as machinists prefer them.
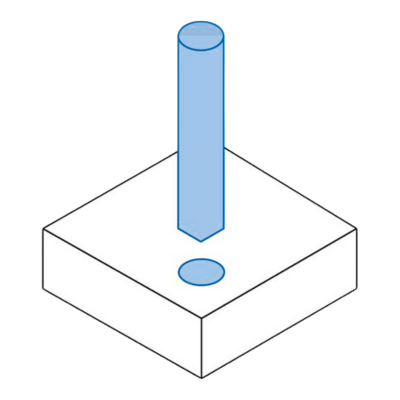
Holes
Recommended Diameter | Recommended Depth |
Standard drill bill (or larger than 1 mm) | 4x nominal diameter (10x nominal diameter is common) |
End mill tools feature a flat or slightly rounded bottom edge. For different floor radii, ball end tools are used. Following the recommended values is a best practice, as machinists prefer them. To machine holes quickly and accurately, use standard drill bits or end mills. This eliminates the need for extra tools to fit non-standard sizes.
For holes with non-standard diameters, use an end mill tool. Follow the maximum cavity depth guidelines. If a hole is deeper than usual, use specialized drill bits with at least a 3mm diameter. Blind holes drilled have a conical floor at a 135-degree angle, while those machined with an end mill tool have a flat floor.
In CNC machining, there is no specific preference for using through holes or blind holes.
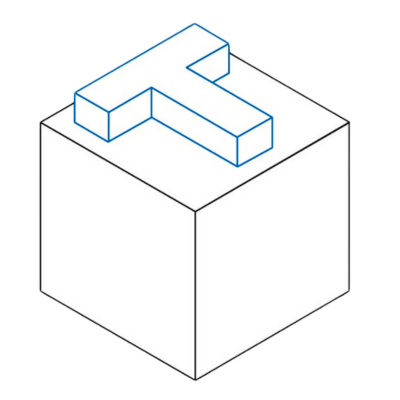
Lettering
Text can be added to the machined part by painting or laser engraving during finishing. If you need the text to be machined, follow these guidelines:
- Opt for engraving rather than embossing to minimize material removal
- Choose 20-point Sans Serif fonts (many CNC machines have pre-programmed fonts like Arial or Verdana) to engrave or letter your parts
What are the key considerations when designing parts for low-volume CNC machining?
In low-volume production, it's crucial to be flexible and customizable. Designers should aim to reduce setup times, use adaptable tools, and refine designs for swift changes and adjustments.
What are the key considerations when designing parts for high-volume CNC machining?
In high-volume production, it's vital to be efficient and consistent. Designers should aim to streamline designs for automation, shorten production times, and maintain quality and consistency.
How does part complexity affect design for low-volume CNC machining?
CNC machines make it easier to handle complex parts in low-volume production. Still, designers should simplify designs to save on machining time and costs.
How does part complexity affect design for high-volume CNC machining?
In high-volume production, complex parts can slow down the process and lower efficiency. Designers should focus on simplifying designs and reducing intricate features to make machining more efficient.
What role does material selection play in designing parts for low-volume CNC machining?
Material selection for low-volume production should consider machinability, cost, and availability. Designers can choose materials that are easier to machine and more cost-effective for smaller batches.
What role does material selection play in designing parts for high-volume CNC machining?
For high-volume production, choose materials that are consistent, durable, and cost-effective. Select materials that can endure repeated machining while maintaining quality in large quantities.
How can design optimization reduce costs in low-volume CNC machining?
Optimizing designs for low-volume production helps cut costs by reducing material waste, streamlining setups, and using standard tools. This efficiency results in faster turnaround times and lower expenses.
How can design optimization reduce costs in high-volume CNC machining?
Design optimization for high-volume production can reduce costs by streamlining machining processes, reducing cycle times, and minimizing tool wear. Efficient designs can lead to higher throughput and lower per-part costs.
What are common challenges in designing parts for low-volume CNC machining?
Key challenges include managing setup times, adapting to design changes, and maintaining quality control. Designers need to be flexible and quick to respond to changing requirements.
What are common challenges in designing parts for high-volume CNC machining?
Key challenges include ensuring consistency, managing tool wear, and improving cycle times. Designers need to prioritize repeatability and efficiency to meet production goals.
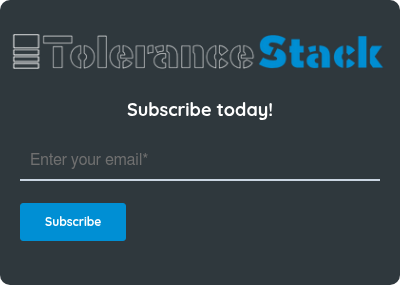
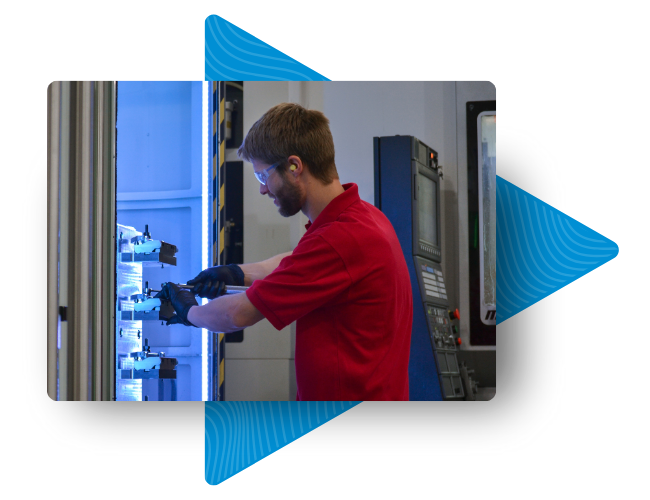
Let's connect
Want to learn more about our CNC machining services? Schedule a time to speak with our team.